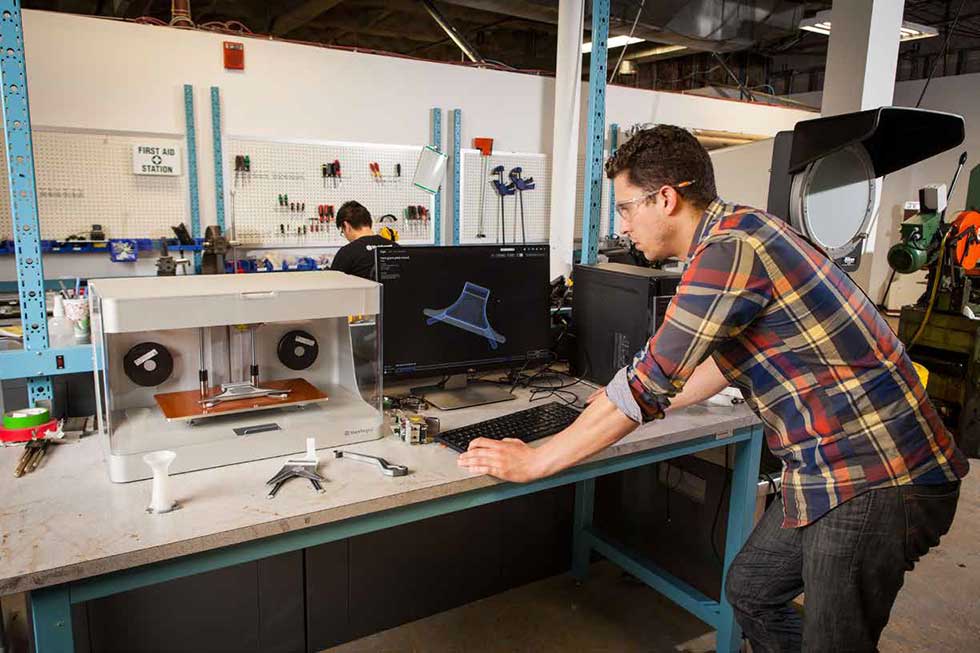
What an interesting time the last few years have been! As we dive deeper into 2021, it occurred to us that not everyone knew what Markforged had been up to in the last year. Especially when it came to important gains and improvements around new materials, increased build volume, and heightened data security. So we threw together this blog to give you that overview of the value-added things Markforged continues to bring to the table time and time again as they innovate.
1. Preventative Maintenance Tracker
As educators and advisors around 3D Printing technology, we want you to protect your investment and make sure you get the most of it. Just like any other piece of machinery or operational equipment, your Markforged 3D Printer needs a little care and TLC too.
But at Markforged, their philosophy with all that they do is to make the process easy and streamlined. With preventative maintenance, they take the guesswork away. With 2020’s Preventative Maintenance Tracker, you can make sure your printer is running seamlessly and efficiently with every build!
2. ISO 27001 Certification in Data Security
Unique to Markforged among all 3D Printing providers, and a feature they get audited to upkeep, is their ISO 27001 Certification in Data Security.
The ISO / IEC 27001 certification means that Markforged has met international standards in ensuring privacy, confidentiality, and integrity of the entire Markforged 3D Printing ecosystem. It means Markforged has a best-in-class Eiger cloud additive manufacturing platform, 3D printing hardware, fleet management software, and information governance policies.
What this means is global companies can quickly adopt additive manufacturing whether they’re in production assembly, defense, military, R&D, and aerospace. They are focused on protecting critical and sensitive information in a way that guarantees management and mitigation of risks. ISO / IEC 27001 is an Information Security Management System (ISMS) standard published in October 2013 by the International Organization for Standardization (ISO) and the International Electrotechnical Commission (IEC).
3. Copper & Onyx ESD: New Materials in the Last Year
In December 2020, Markforged announced their new material, Onyx ESD. Onyx ESD is the most advanced polymer Markforged has ever developed. It meets ESD-safe requirements for manufacturers – while offering the same industry leading benefits that their standard Onyx offers. It has an impeccable surface finish, great durability and strength and (like all Onyx materials) can be combined with Markforged’s continuous strand fiber filaments, making it a go-to material for demanding ESD applications.
Onyx ESD is a static-dissipative version of Onyx; Onyx is used by manufacturers for everything from prototypes, to tooling, to end-use parts. Nearly every electronic product you use on a daily basis was built in an ESD-safe environment using ESD-safe tooling. Onyx ESD enables manufacturers to print this tooling on-demand.
In February 2020, Markforged released Pure Copper for their Metal X 3D Printing system. Copper’s prime use is for thermal and electrical designs; but pure copper in the Markforged Metal X system goes beyond the norm. Copper’s high conductivity makes it an ideal material for many heat sinks and heat exchangers, power distribution components such as bus bars, manufacturing equipment including spot welding shanks, antennae for RF communications, and more. It is commonly used as an electrical conductor in power generation, distribution, circuitry and many other types of electrical equipment.
There’s no exposure to powders and no expensive vacuum systems required. This is the only way to reliably, safely, and affordably 3D print a pure copper material. View all of Markforged’s available materials.
4. Leak Tight
Leak Resistant (Alpha) is now out for metals 17-4 PH Stainless Steel and H13 Tool Steel!
5. 15% Increase in Build Volume for Mark Two Customers
Always on the lookout to improve throughput and maximize the build volume of their printers, Markforged was able to increase the build volume of the Mark Two desktop printer by 15% with software updates. This means new AND existing Mark Two customers benefit from 15% more capacity on from the same machine, allowing for even larger part creation and higher throughput!
6. Exposed Infill (Alpha), The Ulitmate in lightweight Robotic Parts
Infill serves as the internal support structure for the part, so without it, nothing would be holding the walls or shells together! Infill adds stiffness to the part and prevents the walls of a part from deforming and the roof from caving in. By relying on the strength of the infill and walls, Markforged has unlocked the ability to produce parts with no typical roof or floor layers, exposing the internal cavities of the part. This allows for incredibly fast wash times, reduced print times, and reduced material usage while making lightweight metal 3D printed parts even lighter! Producing strong parts that often could not be produced using any other manufacturing method.
7. Sinter-2 Express Run
The Sinter-2 Express Run is now available for small batch 17-4 Stainless Steel parts! This is ideal for small batches of end-use or prototype parts printed in 17-4 where a standard sinter run may not be economical or when time is of the essence. When running an express run, up to 250 grams of 17-4 parts can be fully sintered with a 70% cost reduction and 45% faster Sintering time when compared to a typical Sinter-2 run. This Express Run unlocks the ability to have sintered parts in-hand next day!
3D Print with Us!
There are a variety of ways you can take advantage of 3D printing. Have a question? We’re always available to talk over the phone, for you to leave a message, or for you to submit a request – just contact us.
Please let us know if you would like to:
- Learn more about Markforged and get educational info emailed to your inbox
- Talk over the phone with our Application Engineer to identify possible applications in your line
- Get a sample part of yours printed to prove material strength and ROI (learn more about what makes Metal printing different and what makes Composite printing a plug-and-play replacement for tooling)
- Learn more about available materials
Anything you need, we’re here to help!
See similar blogs on 3D Printing:
Share
Meet the Author