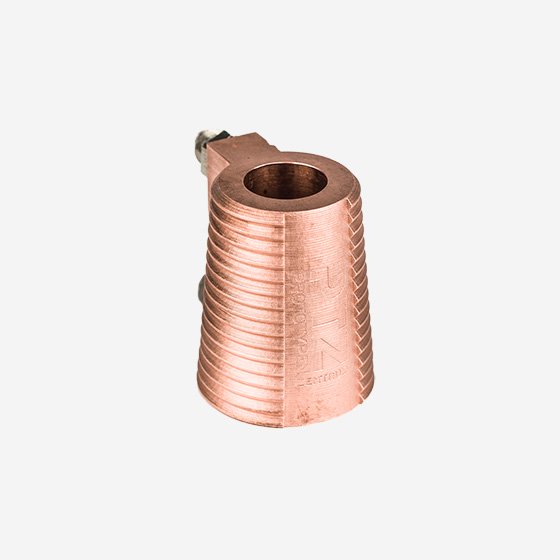
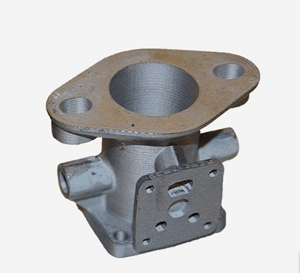
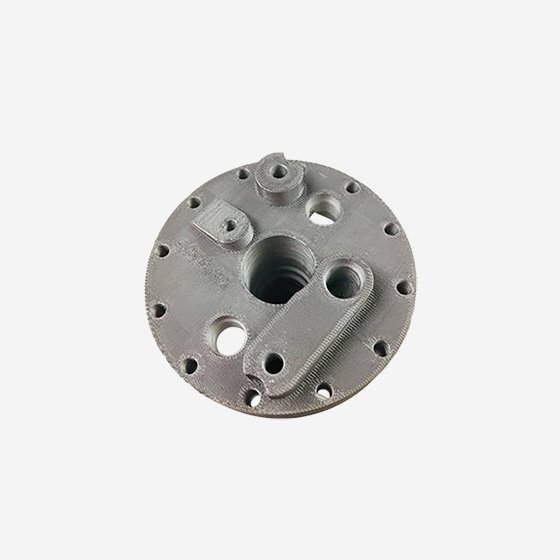
Markforged Metal 3D Printing
From automotive and aerospace, to electronics and manufacturing, these modern manufacturers featured here are 3D printing some pretty revolutionary parts – and doing so in-house out of metal. Explore these 3 practical 3D printing applications from Markforged customers.
Tool Cooler
– Pure Copper
– Company PTZ GmbH
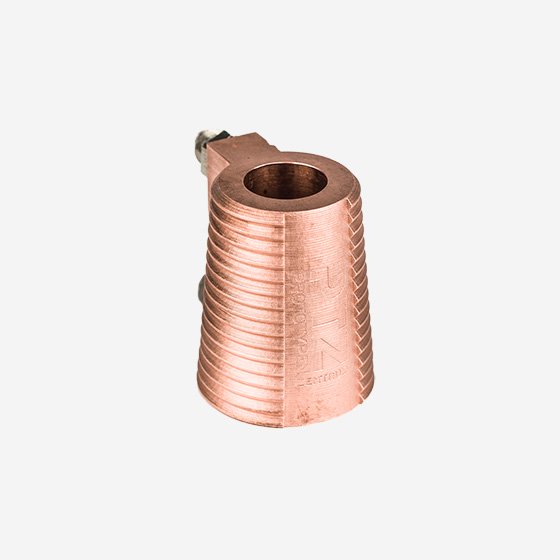
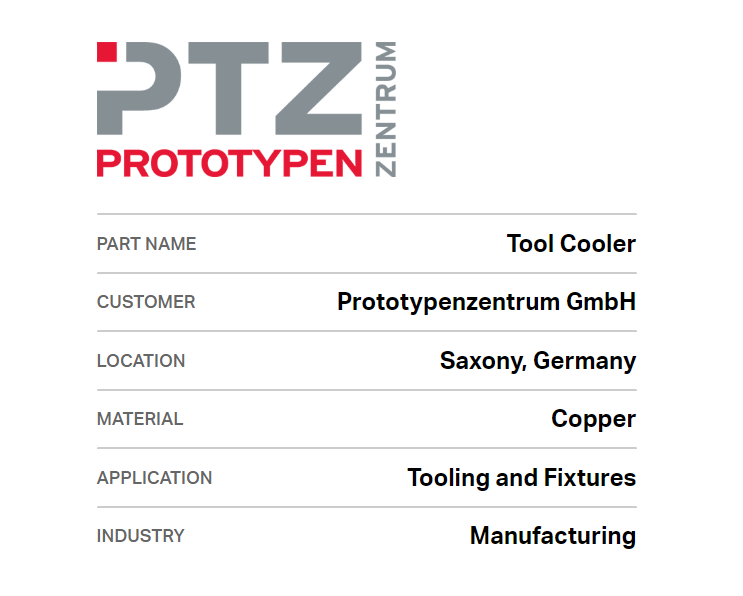
Part & ROI Summary: This tool cooler was originally out of machined aluminum. With a changed design to pure copper, the new tool cooler provides 38% faster cooling than previous designs and eliminates roughly 40 tool changes per day across 2 CNC machines. That saves company PTZ around 111 hours per year. It stands to save PTZ $6,993 each year in machine time alone!
Full Customer Story: Shortened to “PTZ,” the company Prototypenzentrum GmbH, has been producing prototypes for their partners for over 20 years, working in both metal and plastic. They’re highly experienced with several additive manufacturing processes, but were unable to find a solution that worked for some of their most demanding applications until they were able to print with metal on the Markforged Metal X platform.
Originally produced from machined aluminum, the purpose of the cooler is to engage and disengage a cutting tool in the shank of an endmill through thermal expansion and contraction. This is a characteristic component of high-precision mills. The more conductive the cooler, the faster they could reconfigure the tool. The machined aluminum version was simple to produce, but due to thermal performance could not achieve PTZ’s desired cycle times.
Markforged Copper was the perfect fit for PTZ’s problem. Their design featured conformal cooling channels, which would make the tool cooler extremely efficient. This design was impossible to manufacture using traditional methods. Since they already had a design that closely fit the newly-available design space for the Metal X, they were in a great position to bring their idea to life in highly-conductive copper.
The new tool cooler could hold up to the cooling medium and provide 38% faster cooling than previous designs. By eliminating roughly 40 tool changes per day across two CNC machines, it would also save 111 hours per year. Given the average hourly machine rate, it stands to save PTZ $6,993 each year in machine time alone. Offering both the lowest cost and the highest performing materials made Markforged technology the only logical choice for the tooler cooler. The team plans to use Markforged Copper to develop electrotechnical parts for automotive devices.
Replica Carburetor
– Stainless Steel 3D Printed Part
– Company Tecron Automotive
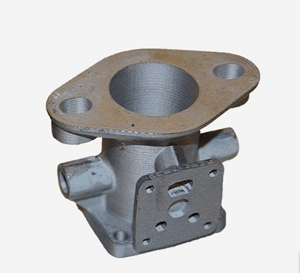
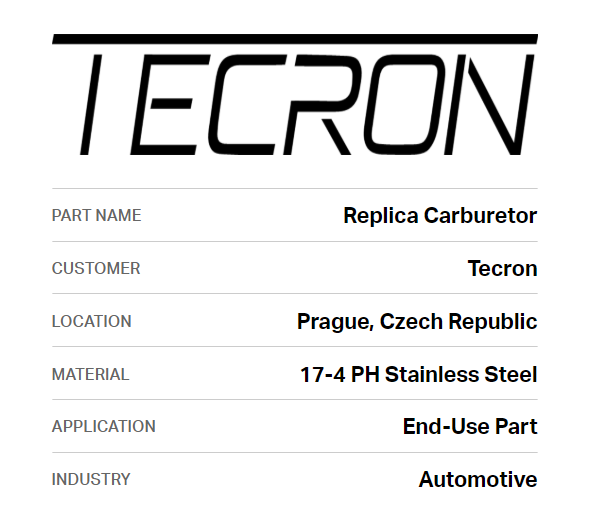
Part Summary: Tecron, a manufacturer of vintage race car legacy parts, was drawn to Markforged metal 3D printing after meeting their evaluation criteria. They replicated an original part for a customer that needed a discontinued race car carburetor redesigned, and printed a cost-effective 17-4 PH Stainless Steel solution!
Full Customer Story: Tecron provides manufacturing services to European automotive companies. They focus on legacy parts for vintage race cars — costly low-volume, high-variety production. They’ve produced parts with original instruments from the ’70s and ’90s. Tecron was drawn specifically to metal printing by Markforged 3D printers. Škoda Motor is Tecron’s customer that reconstructs vintage cars, and needed to manufacture a race car carburetor that had long been unavailable. The 3 part assembly was originally made with die-casting methods until the sole supplier discontinued and the original die was lost. Tecron was able to replicate the original part with some redesign, and print a cost-effective metal solution.
Additionally, Czech Aerospace Research Centre (VZLU) partnered with Tecron for help with validation of new concepts. VZLU was having difficulty producing cost-effective components in a new wing design. The nozzle concept they have, has intricate features and a narrow slit in the design improves overall wing performance. Tecron used the Metal X to produce the part to-spec, with the intricate design left unaltered — and at a fraction of the original cost.
Diesel Fuel Injector Adapter
– Stainless Steel
– Company Sandia National Labs
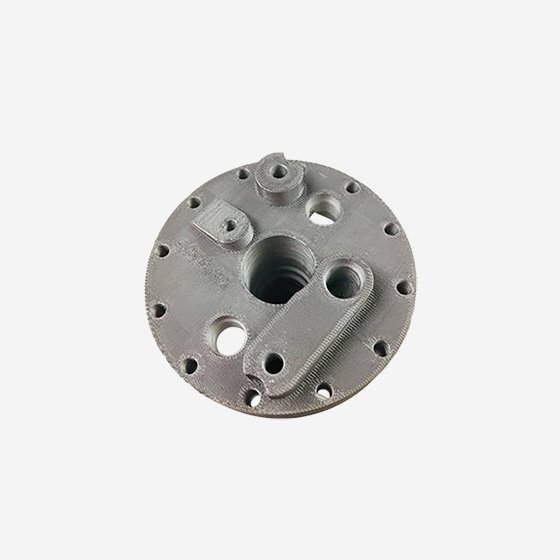
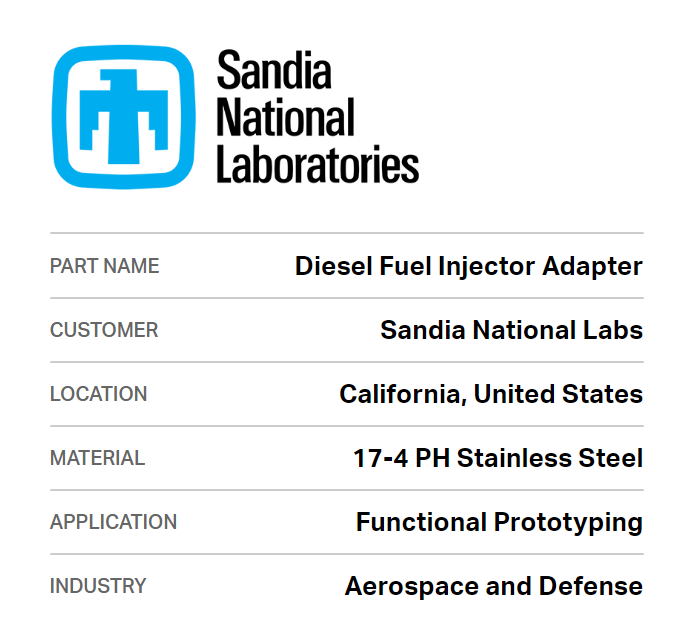
Part Summary: This diesel fuel injector adapter is 3D printed in 17-4 PH Stainless Steel. Sandia National Labs moved away from outsourced laser sintering and CNC machining (weeks of waiting and costly parts). Through Markforged, they now print metal in-house and on their schedule!
Full Customer Story: Sandia National Labs improves the efficiency of internal combustion engines. The team produces physical simulations of diesel fuel flow scenarios and run up against physical manufacturing constraints. Needing internal geometries for optimal flow, they rely on 3rd party laser sintering and CNC machining, taking weeks or months to get the final part. And that part may cost tens of thousands of dollars.
Through Markforged, Sandia has simplified their workflow: design, print, then post-process with an internal CNC. Markforged was the first solution that could print metal in-house while conforming to their Environmental Health & Safety (EHS) requirements. This new capacity means lower lead times and more high-quality iterations.
Sandia printed this diesel fuel injector adapter in 17-4 PH Stainless Steel to test parameters established by the Engine Combustion Network (ECN). What used to need specialized and expensive equipment is now fabricated on a Markforged printer. Once finished, critical surfaces and mating features are fine-tuned on a CNC mill.
Sandia is now investigating the feasibility of printing more high-impact components using other Markforged materials, like high-temperature valves and nozzles in 3D printed Inconel 625, along with other critical fixturing components for imagining.
About 3D Printing with GSC
There are a variety of ways you can take advantage of 3D printing. Have a question? We’re always available to talk over the phone, for you to leave a message, or for you to submit a request – just contact us.
Please let us know if you would like to:
- Learn more about Markforged and get educational info emailed to your inbox
- Talk over the phone with our Application Engineer to identify possible applications in your line
- Get a sample part of yours printed to prove material strength and ROI (learn more about what makes Metal printing different)
- Virtually attend a free, short-and-sweet webinar with our 3D printing team
Anything you need, we’re here to help!
Share
Meet the Author