Introduction to Valmet (Formerly J&L Fiber)
Who is Valmet? Valmet, North America supports the pulp, paper, and energy industries with 1,334 employees and a network of 18 service, production, and sales units across the US, Canada, and Mexico.
A manufacturer and supplier of low-consistency refiner segments (important wear parts used in pulp and paper production), they supply these high-consistency refiner segments for use in thermomechanical pulping and medium density fiberboard (MDF) refining.
Partnership with GSC on 3D Printing
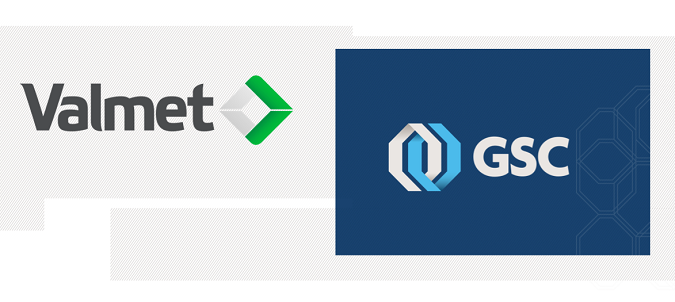
Valmet found something that surprised them. The benefit of introducing a Markforged Industrial 3D printer in-house at their foundry gave them quicker and easier production of their patterns, gates, and risers. They also utilized this new technology to repair equipment, create manufacturing aids, and maintenance items. They revamped age-old foundry processes to be more convenient and more cost-saving than previously thought possible.
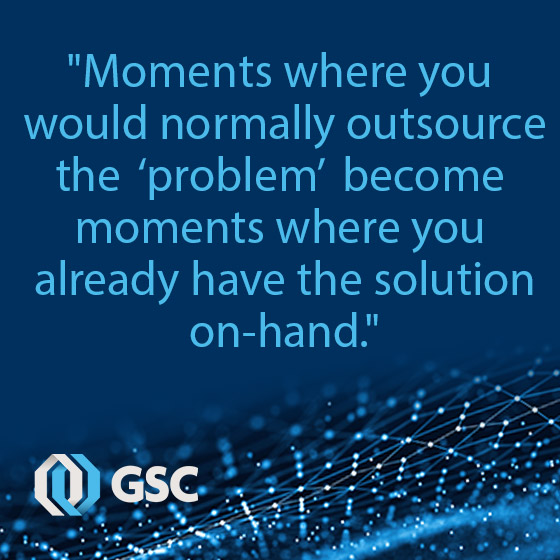
Valmet did the following:
- Rethought materials (from wood, to onyx).
- Created their own line of accessories and manufacturing aids.
- Fostered more creativity and thoughtful design. They brought what would have been custom, out-sourced parts in-house and made them more functional and cost effective.
- Saved themselves from critical down time when the line went down due to part failure. Replacement parts were printed on-the-fly allowing them to stay operating and saved 16 hours of production.
Here follow those applications that made all the difference.
Provided a Quick Save for Line Down-Time: Reverse Engineered Critical Pump Part
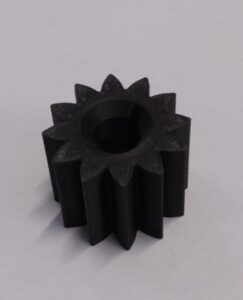
Earlier this year, a gear within Valmet’s resin pump failed, shutting down the line. If they had ordered a replacement part, it would have been 24 hours to wait to overnight the $72 replacement part, leaving them down for at least 2 shifts. That $72 part would end up costing them thousands of dollars in downtime. By taking a few measurements to quickly reverse engineer the failed part, Valmet was able to design a quick replacement that printed in a few hours. The part worked perfectly, got the line back up and running within the same shift, and is still being used in the pump as of this writing.
Traditional Process:
- Unfortunate experience that happens to the best of us; unexpected line shut down for over two shifts
3D Printing Process:
- Part was reverse engineered and printed in just a few hours
- Part was only needed for 1 day, but the part has been running for over 5 weeks as of this writing with no issues
Moments where you would normally outsource the ‘problem’ become moments where you already have the solution on-hand moving forward. Being able to print parts like these adds versatility and options when a production line or a process is shut down due to part failure.
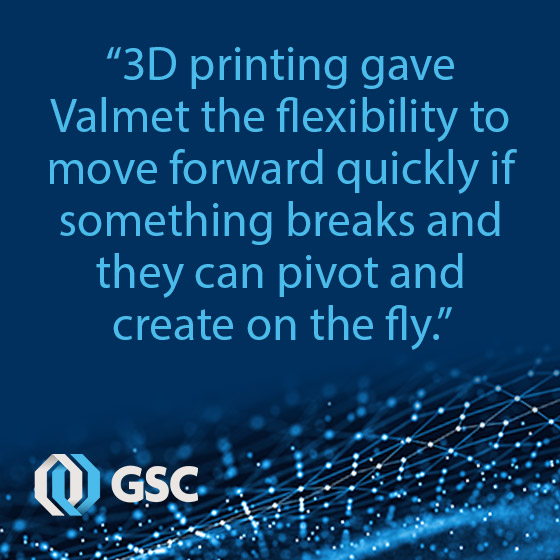
Replace Worn Gates & Risers with Onyx Printed Versions
Traditional Process:
- Full day in pattern shop. Additional time for mounting, filling holes, adding leather fillets
- Aluminum or red board materials are significantly higher cost and require extensive machining
3D Printing Process:
- Prints in 1 day
- Fraction of material cost
- No touch time for creation, more durable, resists blasting process, lasts longer
The ability to replace gates and risers is what justified bringing Markforged 3D printing in-house. Valmet saw significant time savings by producing these parts additively and a fraction of the material costs. As sets wear out or break, they can print a new one for just-in-time inventory. Using the Composite Materials, the gates, risers, and heels are as durable as their aluminum / red board materials.
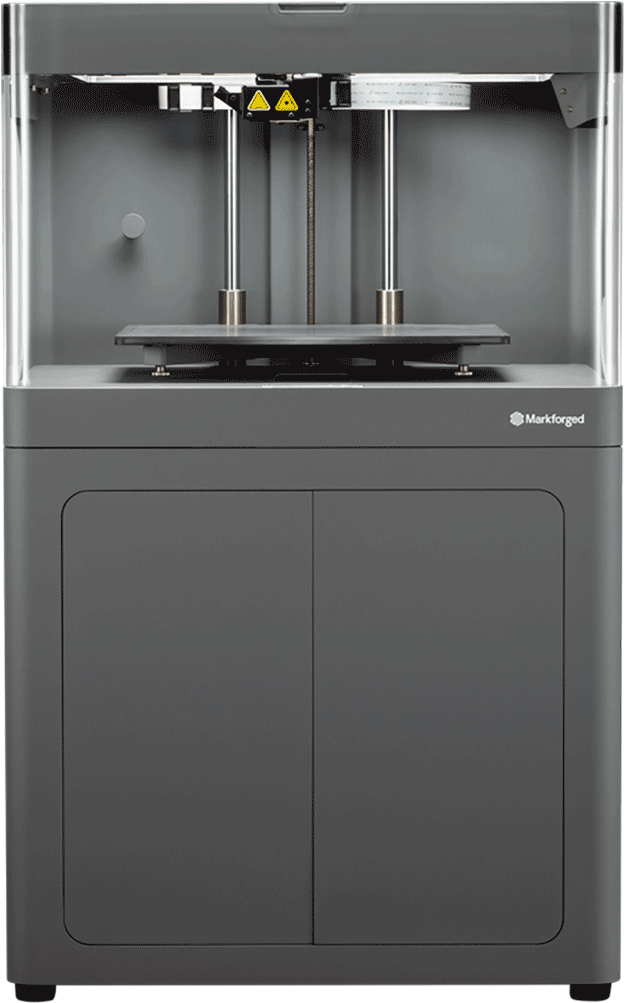
Markforged composites have proven to resist the blasting process and last longer; they’ve retained high strength during the cleaning process. Valmet ultimately purchased the X3 Industrial printer for its larger print volume and higher resolution. With the ability to print at layer resolutions as fine as 50 micron, the Industrial Series printer works exceptionally well for parts requiring incredibly smooth and detailed surface finishes. It saves time and labor versus the traditional process that required at least a full day in the pattern shop to create aluminum or red board gating, which included the tasks of mounting, filling holes, and adding leather fillets.
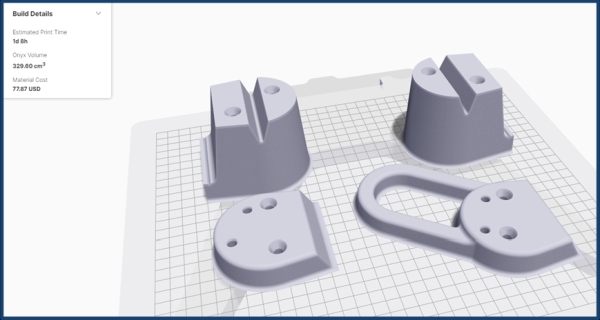
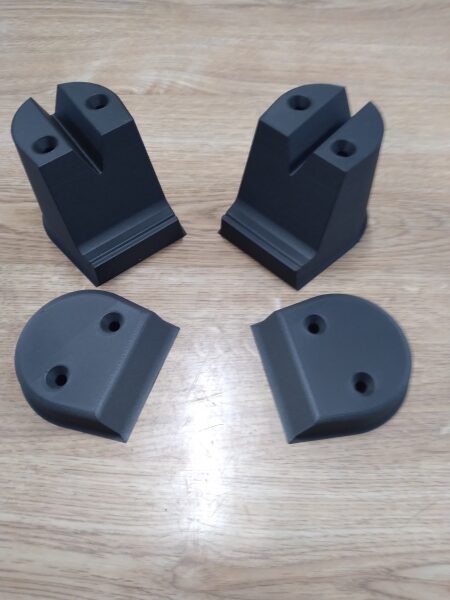
Manufacturing Aid Production: 17 Days to 2 Days for In-House Production of Sprue Former
Traditional Process:
- Traditional aluminum part cost at $340
- Lead time at 2 and a half weeks
- Reliance on outside sources for production
3D Printing Process:
- 3D printed part cost at $54
- Lead time cut to 1 day and ten hours (34 hours)
- Production remains in-house, reducing dependence on external supply chains and adding tremendous flexibility
3D printing gave Valmet the flexibility to move forward quickly if something breaks and they can innovate and create on the fly. They can pivot if a problem comes up or a design change is required. Bringing part production in-house changed the way Valmet thinks about their process, and allows independence and flexibility they had never thought possible. The fact that the 3D printed part cost was less (1/5th the traditional part cost) was just icing on the cake.
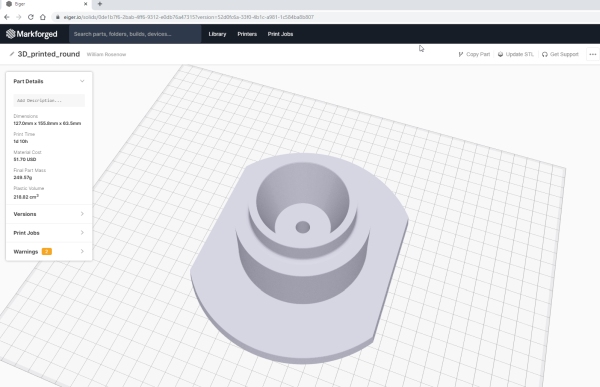
Sprue Former in Process
Magnet installed in 3D printed former and placed on sprue pin on equipment. First mold is made, and sprue former is attached to blow head for the rest of the run.
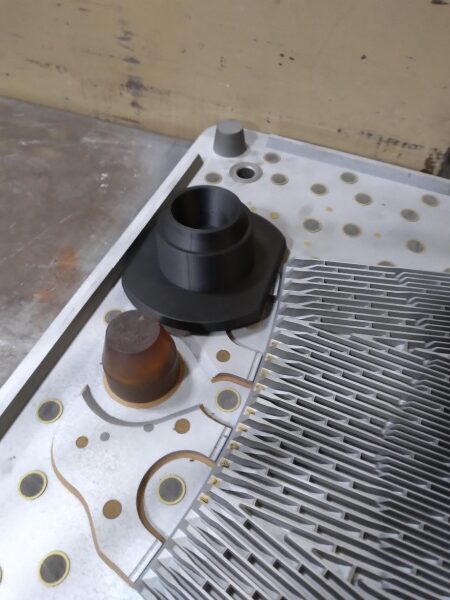
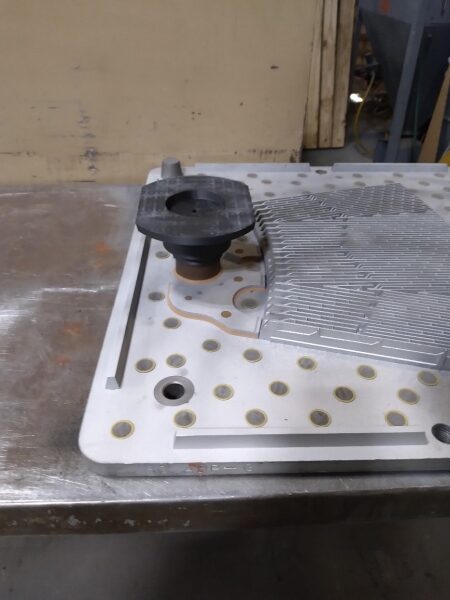
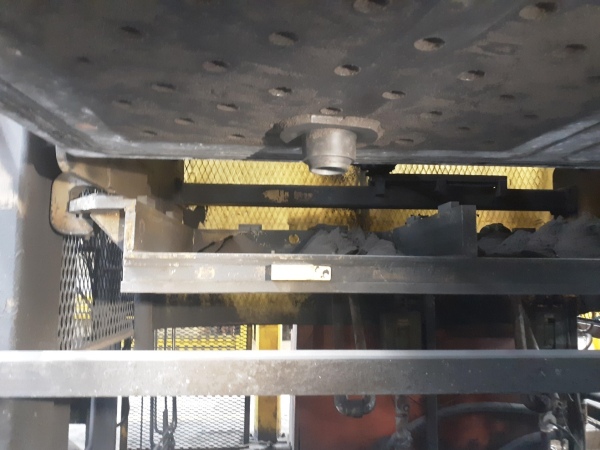
“One great thing about the 3D printed former versus the aluminum is the on-the-fly changes that can be made when the cups come in at the wrong size and the fit is too tight or loose. I make a quick change; in less than 2 days. They don’t have to do extra work to be able to use those cups. That’s 2 days, instead of a week or more for rush aluminum.”
– Bill Rosenow, Design Engineer
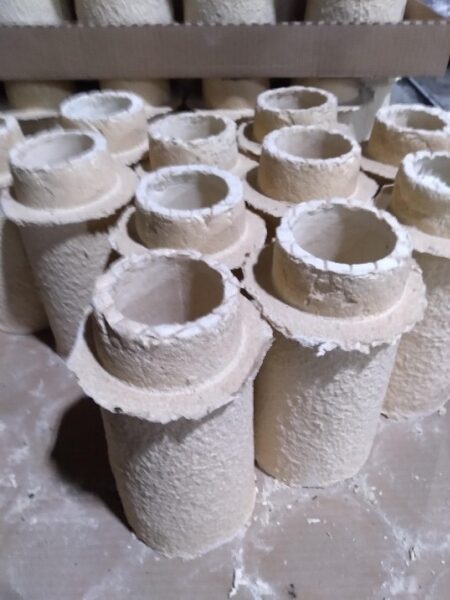
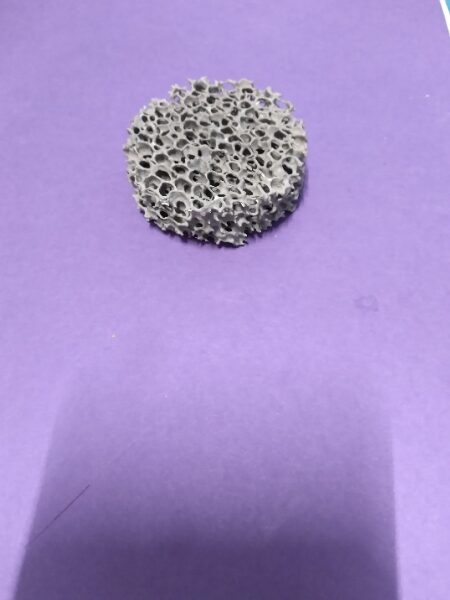
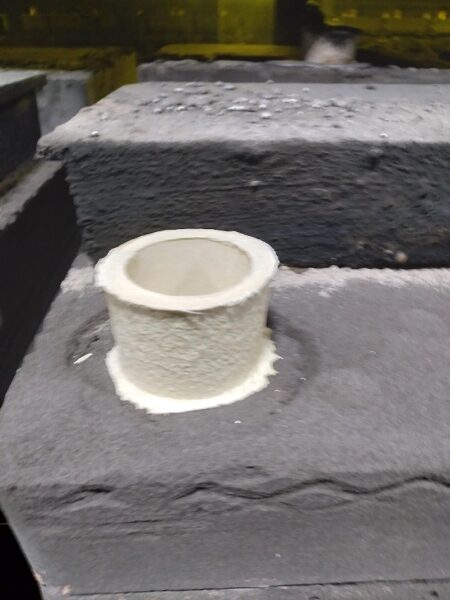
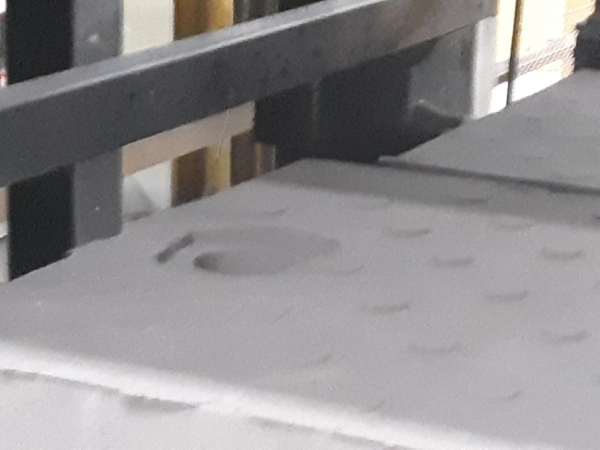
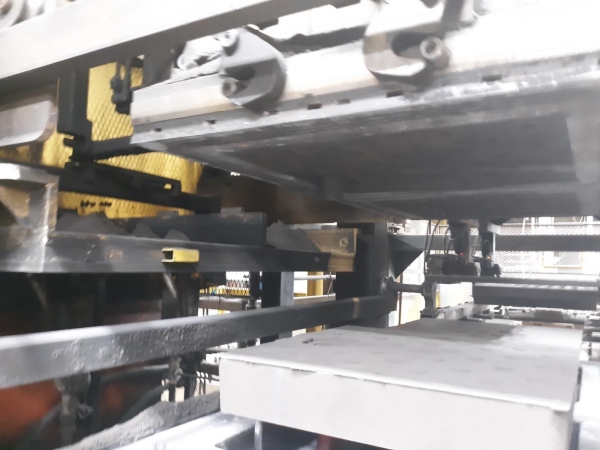
From $176 Per, to $0.35 Per, for Modeling Line Glue Paste Nozzles
Traditional Process:
- Metal Nozzles traditional cost at $176 per
- Traditional lead time is at 4 days
3D Printing Process:
- 3D printing these nozzles cost only $0.35 per
- New lead time is 7 hours per set
By leveraging the printer’s accuracy and the material’s strength, Valmet was able to produce many accessories for their production process that would typically have to be purchased from the OE manufacturer at very high markups. Being able to produce glue paste nozzles for pennies that previously cost $176 per piece is a great example of having your own manufacturing process in-house in the form of an industrial 3D printer.
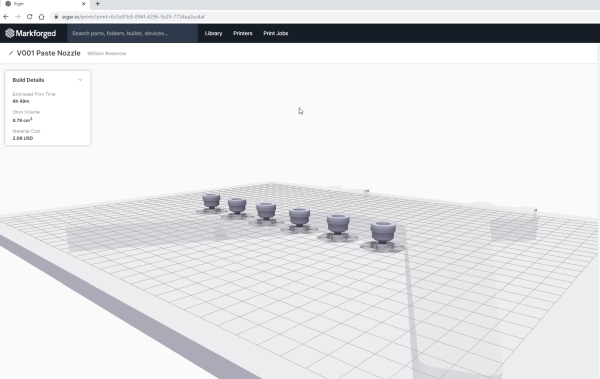
Printing the Master Mold for Urethane Parts & Accessories
To further save time and money, Valmet 3D printed master molds of commonly used pieces to pour highly robust, cost-effective urethane posts. They 3D printed the tools and accessories for the urethane molding process as well.
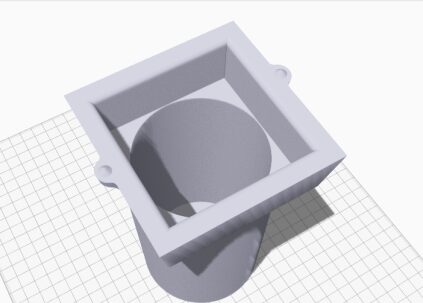
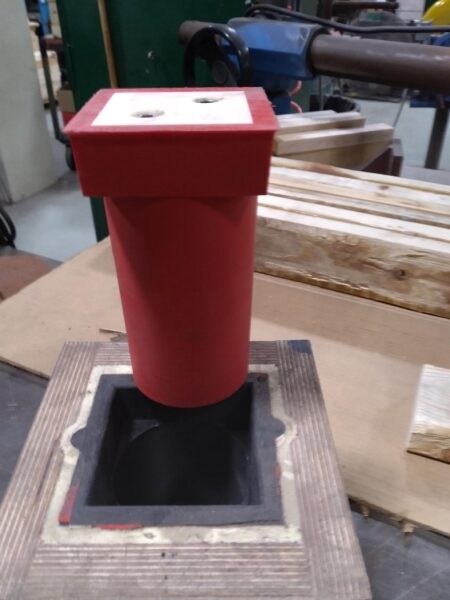
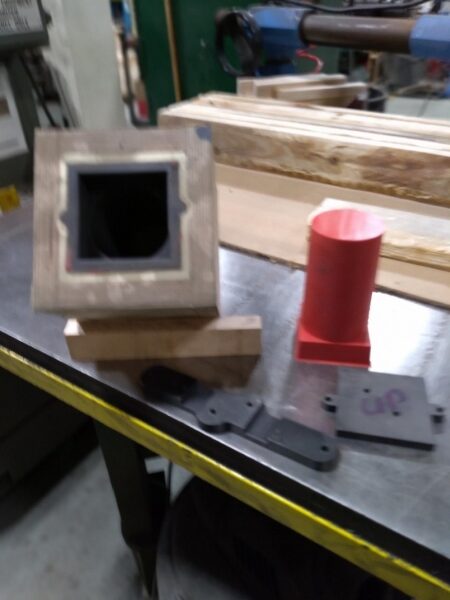
Valmet didn’t originally consider this application when they first brought additive technology in-house, but have since produced new ideas and applications. They can now make as many parts as they want by using a single 3D printed mold.
Efficiency Boost: New 3D Printed Glue Nozzle Steam Cleaner that Cleans 3 Nozzles at Once
Always on the lookout to cheaply and easily improve efficiency, Valmet designed a Nozzle Cleaner that cleans 3 nozzles at the same time, compared to just one nozzle as they had previously. This is a time savings they didn’t expect to see, and would never have been implemented if not for the ability to manufacture their own custom parts in-house. This is just one small example where foundries have the ability to improve many processes in-house to see time, cost, or other savings.
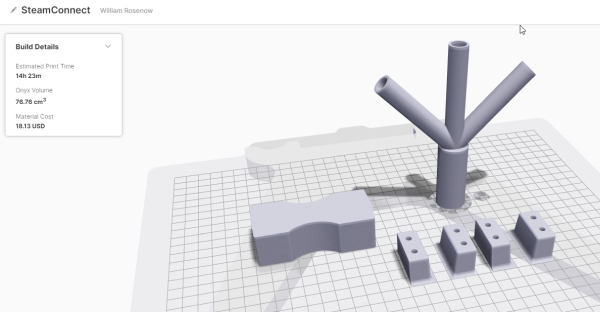
Additional Applications to Consider
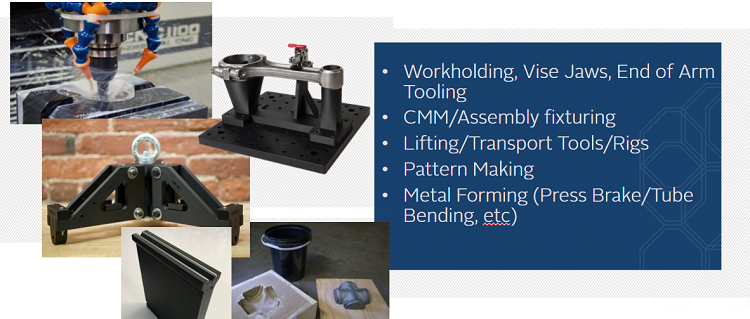
3D Print with Us!
There are a variety of ways you can take advantage of 3D printing. Have a question? We’re always available to talk over the phone, for you to leave a message, or for you to submit a request – just contact us.
Please let us know if you would like to:
- Learn more about Markforged and get educational info emailed to your inbox
- Talk over the phone with our Application Engineer to identify possible applications in your line
- Get a sample part of yours printed to prove material strength and ROI (learn more about what makes Metal printing different and what makes Composite printing a plug-and-play replacement for tooling)
- Learn more about available materials
Anything you need, we’re here to help!
Share
Meet the Author