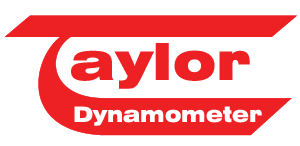
TAYLOR DYNAMOMETER
How Taylor Dynamometer cut days out of their release cycle with SOLIDWORKS PDM Professional
Previous Issues
- The design approval process was paper-based.
- Revision process was not automated.
- File sharing between teams created conflicts.
Improved Process Using SOLIDWORKS PDM Professional
- Single direction flow of data.
- Shortened release cycles.
- File sharing through one common data base.
- Eliminated revision conflicts between teams.
- Ability to complete complicated releases more quickly.
- Seamless file synchronization between remote employees.
Solutions Used:
SOLIDWORKS 3D CAD SOLIDWORKS PDM Professional
Industry:
Dynamometers and Test Equipment for Engine, Towing, & Chassis Systems
Johnson Level purchased the Mark Two industrial grade printer and saw ROI within 9 months. New 3D parts make up their production line including an ultrasonic welding fixture, multiple grippers, packaging prototypes and a new assembly machine.
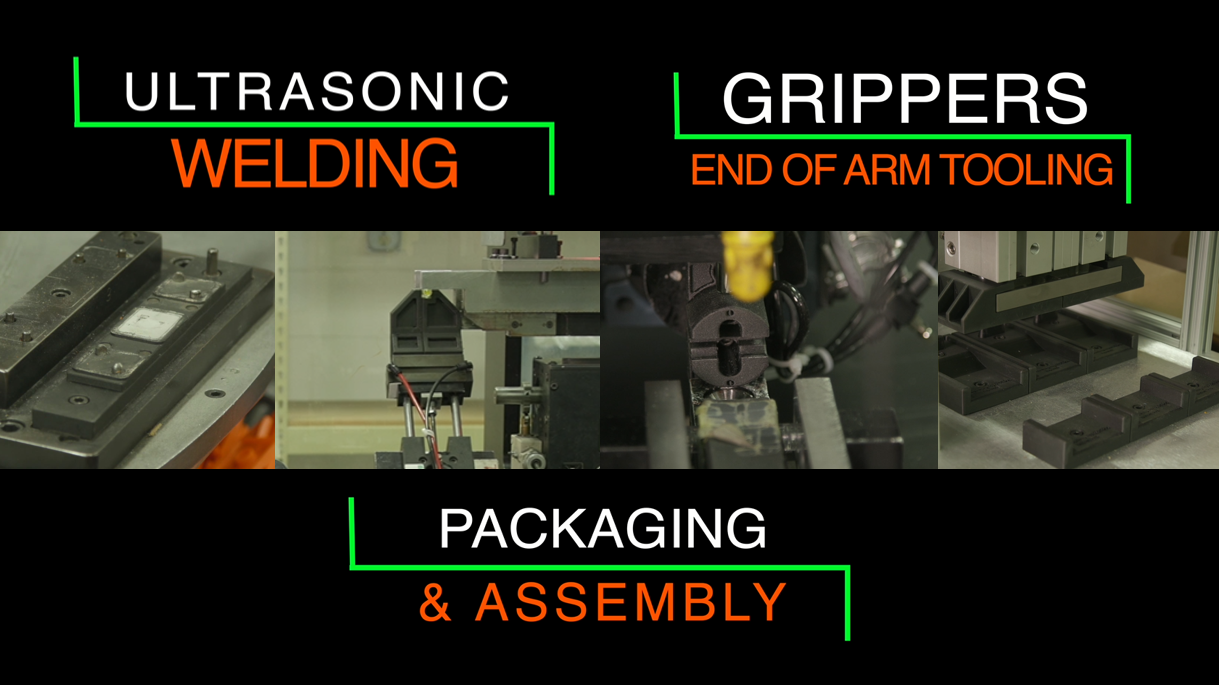
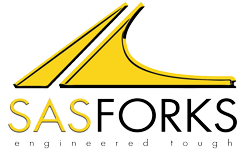
Case Study: From a Broken Part to an Optimal Product Design
The EXTREME Auto Processor
SAS Forks is a manufacturer of attachments for wheel loaders and excavators for use in the auto salvage industry and other severe duty markets. When SAS Forks experienced an issue with a prototype of their EXTREME Auto Processor, SAS Forks turned to SOLIDWORKS Simulation to identify and correct the deficiency in the design.
Through convergence testing in SOLIDWORKS Simulation, SAS Forks was able to determine where the deficiency was in the design and address it. Although the original claw design met all of the basic safety requirements, SAS Forks found that there was high stress in the area in which the claw broke. Once the issue was identified, SAS Forks was able to optimize the design and correct the area of concern. In addition to the new claw design, SAS Forks was also able to fulfill a need for replaceable tips on the unit. By using SOLIDWORKS and SOLIDWORKS Simulation, SAS Forks had the capability and tools necessary to design, test, and order the replaceable tips within 3 days.
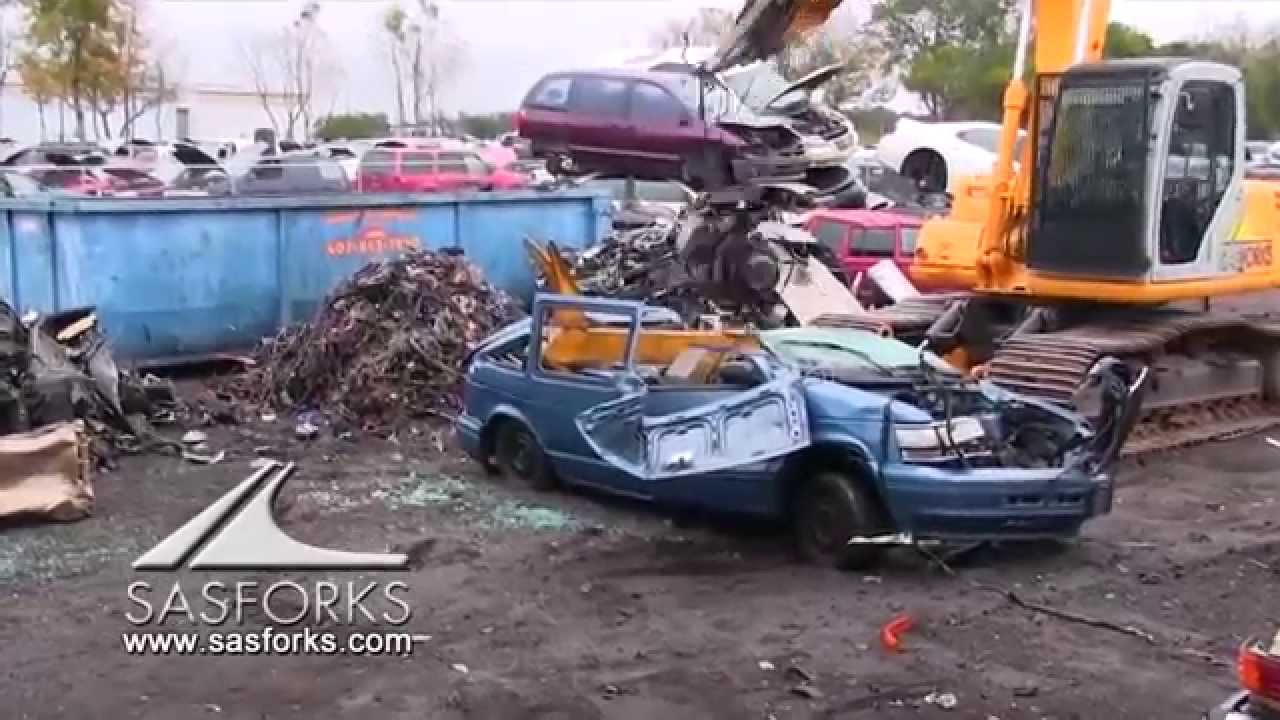
Solutions Used:
Simulation Professional
Website:
sasforks.com
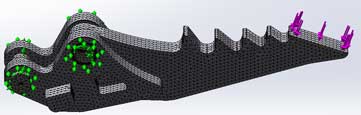
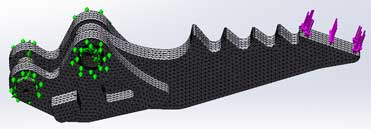
Airstream
Airstream came to GSC during a cost reduction initiative that involved changing the way they manufactured their time-tested camper frames. They wanted to switch to a more cost-effective manufacturing process while also light weighting their components.
Using structural analysis, GSC was able to provide Airstream concrete data about their design changes without the cost and development time associated with traditional prototype and testing processes.