Advanced Validation Testing & Tools
GSC offers comprehensive and sophisticated Finite Element Analysis (FEA) to improve your products by:
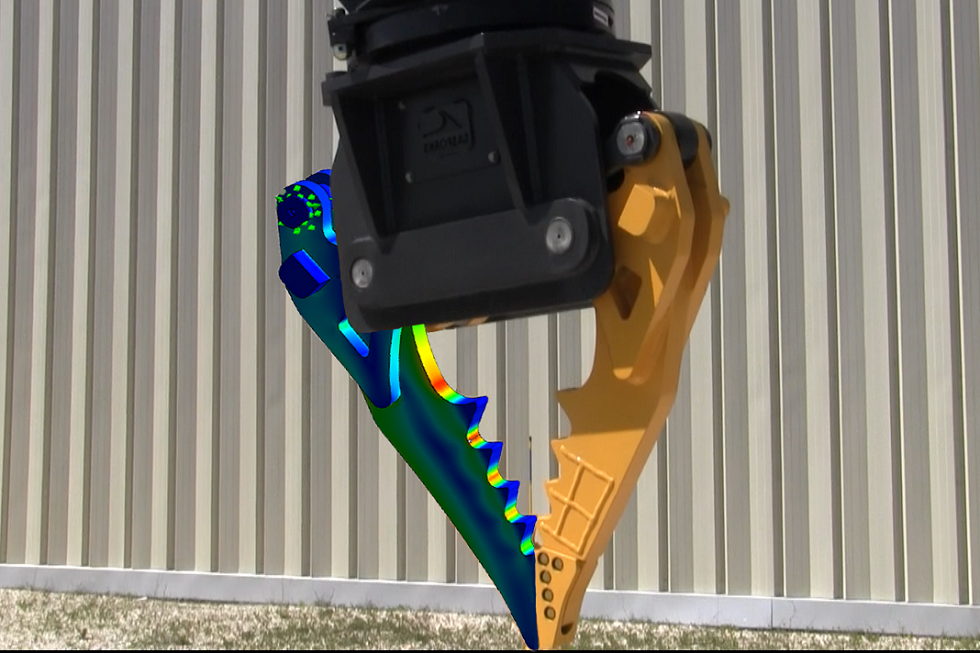
- Studying the performance of your designs for excessive deflections and stresses under dynamic loads.
- Performing nonlinear analysis, including impact, on plastics, rubbers, polymers, and foam.
- Conducting contact analysis coupled with nonlinear materials.
- Evaluating the behavior of composite materials.
Airstream
Customer Success Story
Airstream came to GSC during a cost reduction initiative that involved changing the way they manufactured their time-tested camper frames. They wanted to switch to a more cost-effective manufacturing process while also light weighting their components.
Using structural analysis, GSC was able to provide Airstream concrete data about their design changes without the cost and development time associated with traditional prototype and testing processes.
Our FEA Analysis Includes
Assembly Simulation
We study the interactions of assembly components on-screen, before incurring the costs of physical prototypes. We also simulate static or dynamic loads to evaluate your design’s performance under stress, strain, and displacement.
Mechanism Simulation
We apply a wide variety of physics-based models to simulate real-world operating conditions for your design. Including: checking for colliding parts, output numerical and graphic data of the results, as well as animations of your tests.
Simulate Welded Structures
We ensure your welded structures perform at peak operating conditions. We apply pressure, forces, and bearing loads, then use visualization tools like section plots, ISO clipping, and animation to review the response.
Product Failure Prediction
Save the time and cost of prototyping while creating safer, more durable products. GSC predicts structural failure thresholds due to yielding, overheating, buckling, and fatigue.
Compare & Optimize Alternatives
We determine the best design option by comparing strengths, life, cost, and weight.
Simulate Vibrations
We predict and control vibrations or dynamic responses in your products with a choice of integrated design studies, including Transient study, Harmonic Response study, and Random Response study.
Predict Buckling or Collapse
We virtually apply forces, pressure, gravity, and centrifugal forces to your designs to determine maximum loads before buckling. We study the effects of various materials as well as isotopic and orthotropic factors.
Simulate Heating or Cooling
Thermal analysis capabilities enable you to easily study heat effects on your designs. We simulate thermal boundary conditions, fluid flow, thermal-structural interactions, and radiation effects in high-temperature applications.
Simulate Drop Test or Impact
Save time and cost by reducing the number of physical tests. We perform realistic collision simulation between parts or assemblies.
Simulate Repeated Loading
Simulate, evaluate, and improve a part or assembly that must withstand the rigors of daily operation. We evaluate the differences in your system’s performance to varying speeds or frequencies, and estimates the design life of your entire product.
Nonlinear Dynamics
We thoroughly test and validate your designs with a broad range of advanced capabilities, including: nonlinear displacement analysis, nonlinear buckling analysis, analysis of nonlinear materials, as well as dynamic response analysis of parts and assemblies.
Simulate Plastic & Glass Formation
We simulate your plastic and glass formation in all possible tests and environments. We optimize parts for volume and cost.
WeatherTech
Customer Success Story
WeatherTech worked with GSC to evaluate the usefulness of plastic injection molding analysis on their world renowned floor mats as well as their extremely popular bump step before it came to market.
Using injection molding analysis, GSC was able to help WeatherTech understand all the detailed molding characteristics of their bump step and ensured that the design they had was manufacturable and up to the quality standards that WeatherTech holds themselves to.