The Customer
Amy Vasey is an Automation Design Engineer at HellermannTyton. She has been with the company for 20 years and recently helped introduce and implement 3D printing in their Automation department.
The product development group at HellermannTyton, familiar with additive manufacturing technology, approached Amy’s team, asking if they’d ever considered 3D printing some of their many aluminum parts.
At the time, Vasey and her team weren’t familiar with the technology or where to start. “The product development team was really good at pushing us to start with something small, and that’s what we did.”
Amy and the team realized that additive manufacturing could work in replacing machined parts on end-of-arm tools. Before proceeding, they needed to show their management team that 3D printing was a viable and affordable option. In their early investigation into additive, the team tried to justify getting a printer under $10,000.
“We were trying to change the mindset of how the assembly group thought, how the shop floor thought, how management thought. We had to prove to them that these parts weren’t brittle, that it wasn’t fragile, that it had strength and held tolerances.”
Using an entry-level machine from Raise3d, Amy and her team began to iterate.
The Challenge
“We had our oopsies; I’m not going to lie. We had mistakes. We had parts that failed. We thought, ‘Why are we doing this? Let’s just go back to aluminum. It works.’ But those failures taught us we could do it.” When the Automation team finally saw success with printed parts, they had the confidence to return to the other groups and say, “Hey, this really works. It’s functional. There’s cost savings, time savings, and weight reduction.”
The Solution
Their first application, a deflector, cost $195 to machine, taking two to four weeks to produce. In this instance, up to six of that particular part could be on one end-of-arm tool. However, by 3D printing the deflector, the team brought the cost down to 81 cents and had the part in hand in less than 4 hours. Additionally, they combined multiple parts into a single printed piece, resulting in fewer parts that required machining.
“We could print any shape,” Amy said. “We weren’t restricted like in a machining process where you have to think about what a machinist can do. With 3D printing, your geometries are pretty endless because there really is no restriction.”
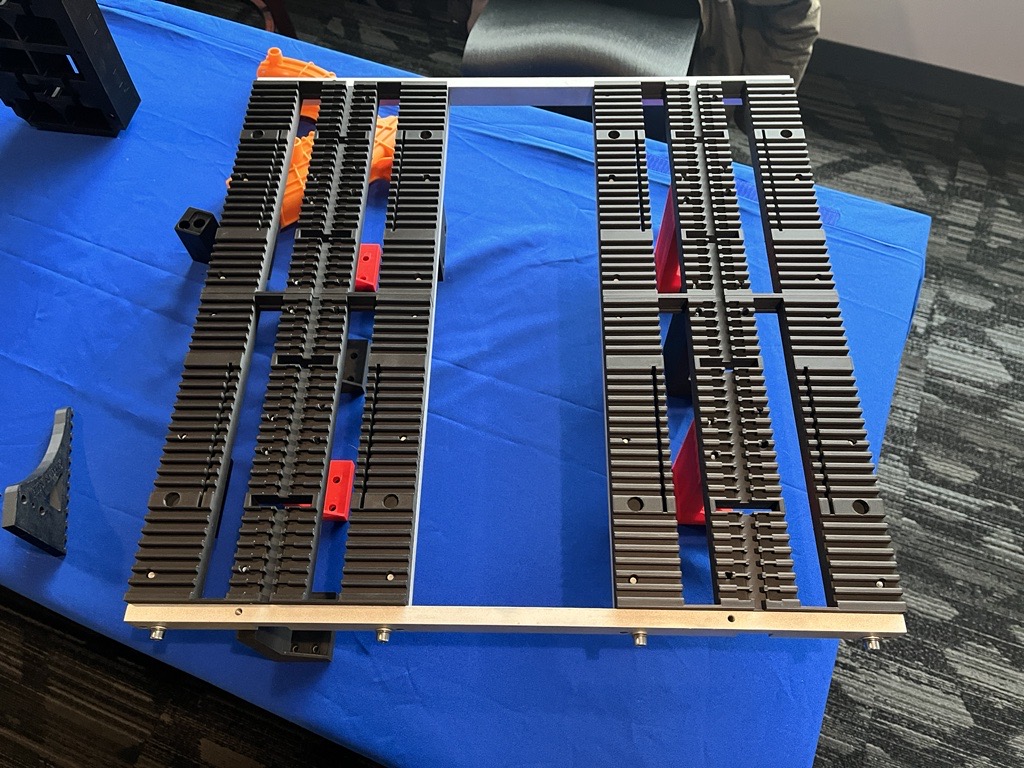
Cost savings are substantial when it comes to end-of-arm tools. While evaluating the capabilities of a Markforged machine, the HellermannTyton team outsourced parts, which saved time and money. But after bringing in a Markforged X7 of their own, they cut the outsourcing numbers down significantly more.
“We went through and figured out every single component cost, time to print, everything. With our own X7, we went from a 42-day machined end-of-arm tool down to a three to four-day additive manufactured tool. The cost went from $28,000 down to $732,” Amy recounted.
While they found a plethora of printing applications, Amy noted that not every component has to be printed. “We still have aluminum and metal components on there for rigidity and for other parts to mount to, which are not 100 percent 3D printed, but are printing darn close – 80 – 85%”
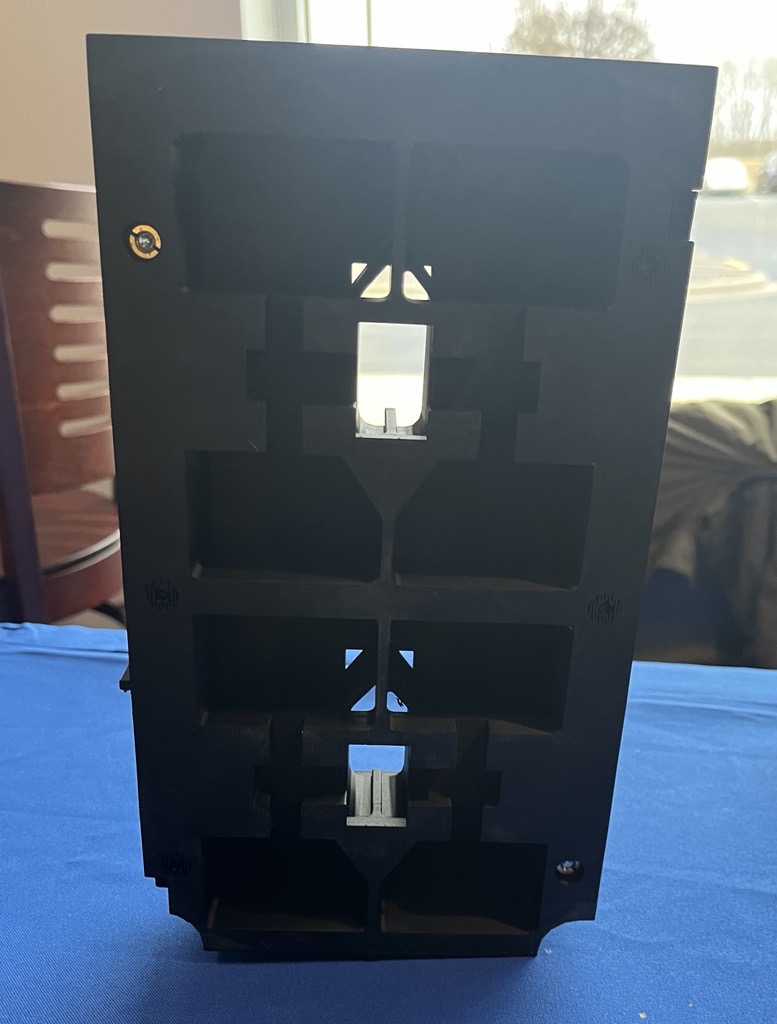
Subsequent Cost Realizations
In addition to the part savings itself, there were also some unrealized costs. HellermannTyton’s end-of-arm tools attach to significantly sized robots. While it sounds like something a sizeable robot could easily handle and has adequately handled, the team realized they could reduce the robot’s size since printed parts were now lighter than what was originally on the robot.
Because the end-of-arm tooling was lighter, the vertical and horizontal travel became a little faster, and in turn, cycle times were reduced. The weight of one particular end-of-arm tool was reduced by 5 pounds, which is a noticeable difference from the machine’s perspective.
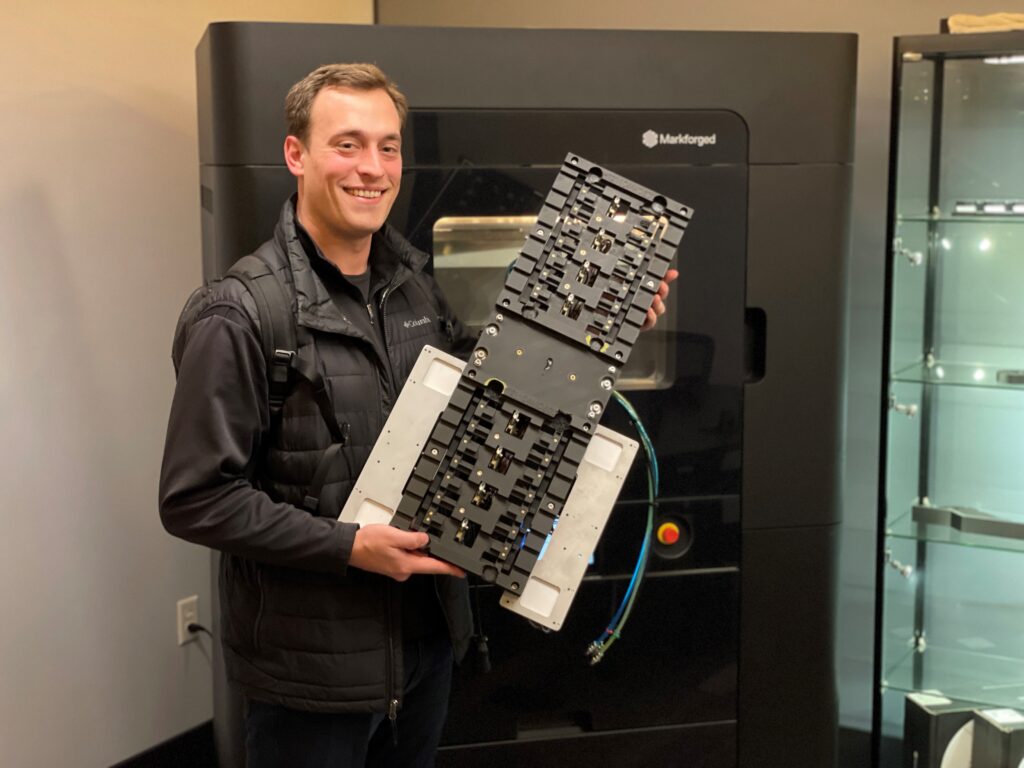
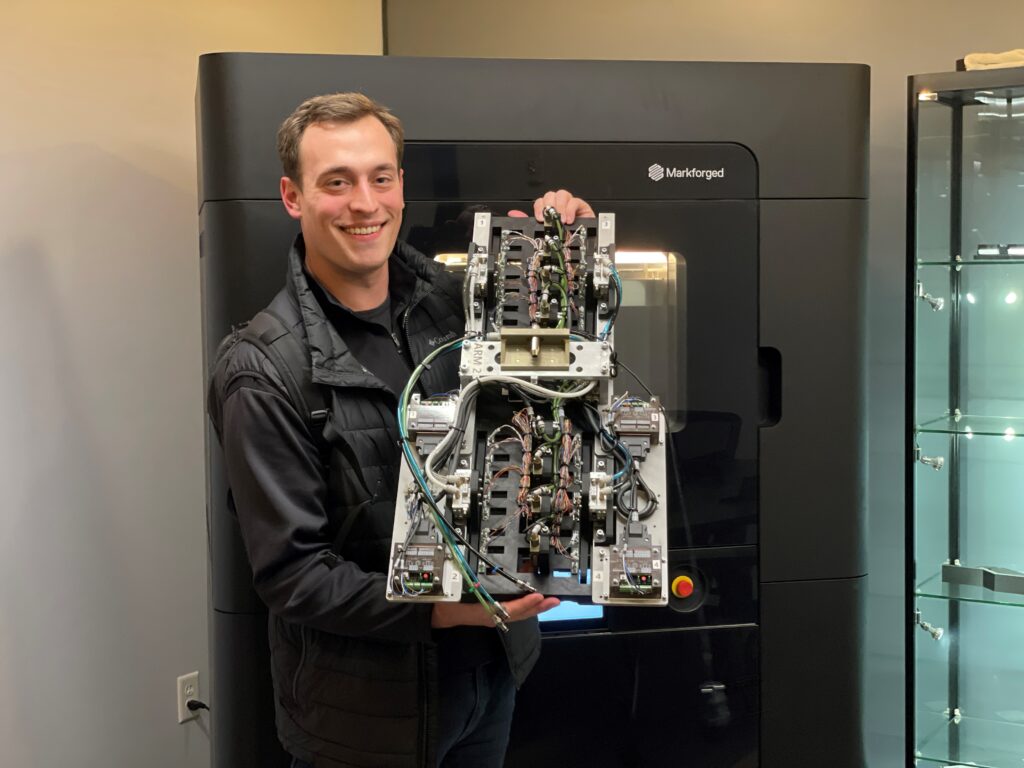
“We’re also reducing downtime on the production floor by utilizing additive. If something breaks, if there’s a part failure, or on rare occasion, the robot runs into the press; we can print a new part in a matter of a day and have it back out on the production floor,” Amy said. “We also reduced our engineering time as well as time to assemble. We’re not spending hours trying to figure out how we’re going to get a really strange geometry machined.”
In just two years, the automation team has progressed from little to no additive manufacturing knowledge to a production ready end-of-arm tool boasting substantial ROI.
“There are never-ending examples of the cost savings that you can realize from something like this. All those are things that people were saying, ‘That stuff is not going to hold up,’ But we stayed with it. I think having a resource like GSC who we could go to and say, ‘We’re not really sure, but can you check and see? Can you help us?’ was a lifesaver. They’re a definite resource if you’re not sure where to start.”
Contact Us
Want to see what 3D printing can do for your company? Contact our additive manufacturing experts or request a 3D printed part.
Share
Meet the Author