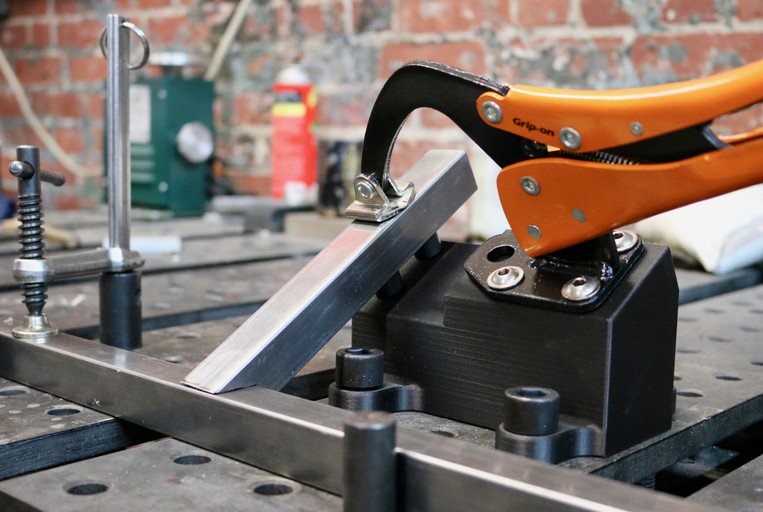
High-Strength 3D Printing for Tooling
The process of designing, prototyping, and fabricating tools for production can be the most expensive and time-consuming portion of the product development cycle. Depending on the complexity of the tool, lead times can be weeks to months and costs soar into the tens of thousands of dollars. As a result, the iteration process can be tedious; any changes to a tool may delay production by months and gouge the budget even further. Fortunately, advances in high-strength 3D printing have brought forth viable solutions.
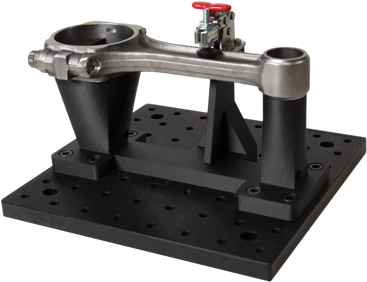
Iterate Quickly
First, 3D printing offers a way to prototype and iterate tooling designs before they go into final production, reducing costs and compressing the development time substantially.
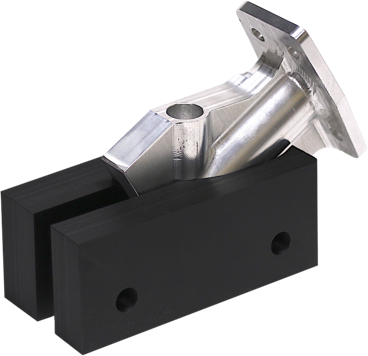
Print Molds, Inserts & Cores
Secondly, many tools themselves can be 3D printed out of composites or metals, simplifying the process even further. Having the ability to print thermoset molds, injection molds, inserts, cores, and other tooling removes the need for CAM, allows for more complex part design without fear of escalating cost, and frees up valuable machine shop resources.
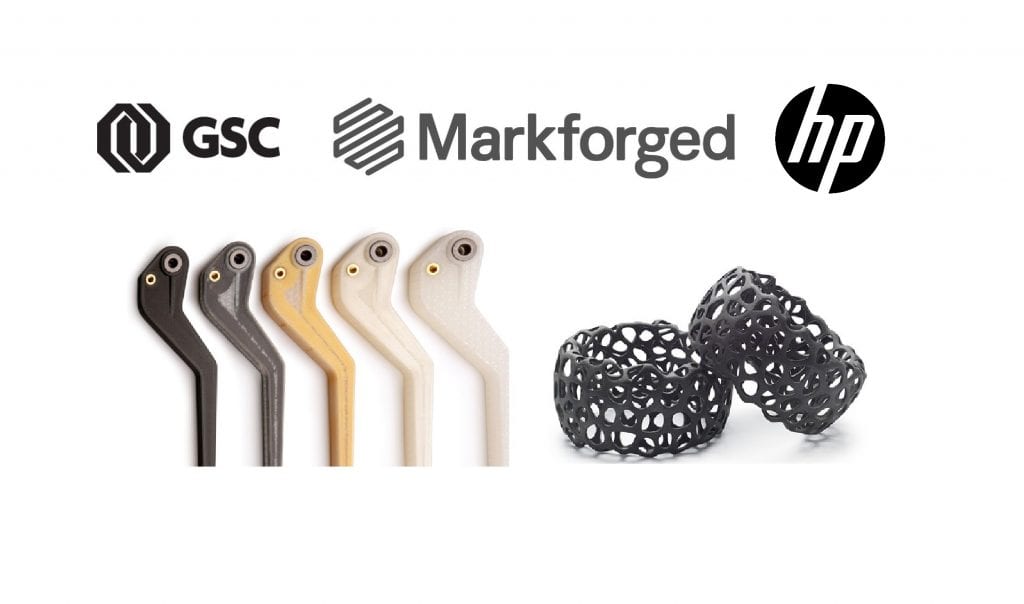
We Can Show You How
If you’re shipping more product but profit isn’t tracking at the same rate as production, these tooling costs could be eating into your bottom line. Visit us at our Germantown Technology Center to learn how 3D printing can lean out your tooling costs and bring your organization into the future of manufacturing! See our machines in action, feel sample printed parts, and hear from our staff, experts in Markforged and HP technology.
Share
Meet the Author