Case Study: From a Broken Part to an Optimal Product Design
The EXTREME Auto Processor
SAS Forks is a manufacturer of attachments for wheel loaders and excavators for use in the auto salvage industry and other severe duty markets. When SAS Forks experienced an issue with a prototype of their EXTREME Auto Processor, they turned to SOLIDWORKS Simulation to identify and correct the deficiency in the design.
Through convergence testing in SOLIDWORKS Simulation, SAS Forks was able to determine where the deficiency was in the design and address it. Although the original claw design met all of the basic safety requirements, SAS Forks found that there was high stress in the area in which the claw broke. Once the issue was identified, SAS Forks was able to optimize the design and correct the area of concern. In addition to the new claw design, they was also able to fulfill a need for replaceable tips on the unit. By using SOLIDWORKS and SOLIDWORKS Simulation, they had the capability and tools necessary to design, test, and order the replaceable tips within 3 days.
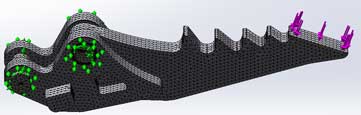
Old Design
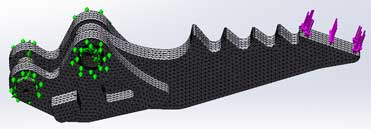
New Design
Share
Meet the Author