Challenge
The process of designing, prototyping, and fabricating tools for production can be the most expensive and time-consuming portion of the product development cycle. Lead times can be weeks to months; any changes to a tool may delay production by months and drive costs even higher. When you need custom molds for low-volume production runs, 3D printed molds can be an affordable, fast alternative.
Solution
3D printing involves no tooling and little to no manufacturing preparation, making it ideal if you need to achieve fast turnaround times without sacrificing complexity or accuracy. Print customized electrodes unattended using the Metal X and charge them with electricity using a die-sinking EDM machine to create a mold. Or you can rapidly create 3D printed molds using materials that withstand high temperatures and extreme environments to replace traditional thermoset molding methods.
Impact
Save Money: Cut costs by reducing the labor and material/scrap it takes to create a customized mold.
Save Time: Create next-day molds that can withstand extreme environments and are robust in high temperatures.
Easily Make Customized Molds: Create custom and complex molds for specific applications and have them ready to use in just a few days.
Customer Success Story:
Dynamac uses Markforged for Vacuum Form Molding
FIND THE RIGHT TOOL FOR YOUR APPLICATION
Composite Printing
Solutions
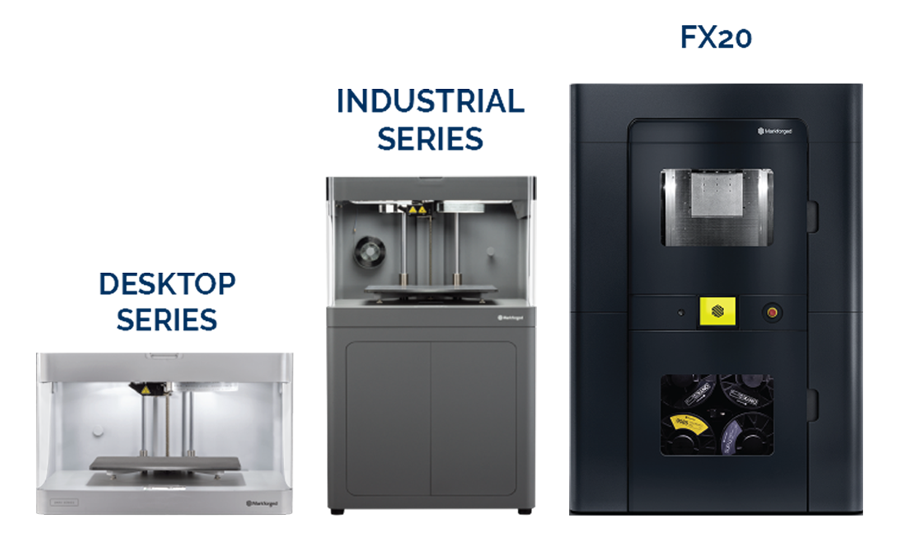
Metal Printing
Solution
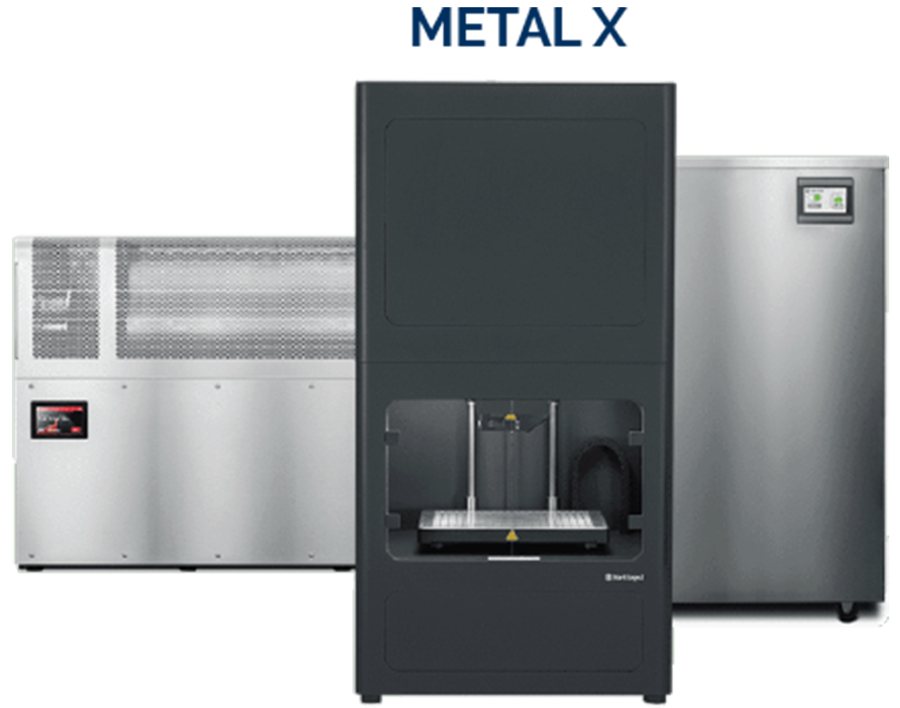