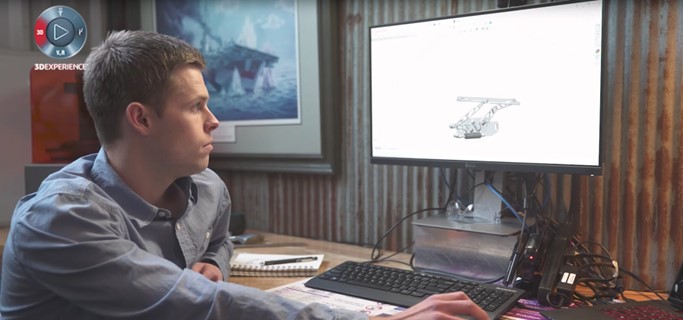
The Looming CAM Skills Crisis
Ask manufacturers about the biggest challenge facing their industry; most will mention a shrinking pool of experienced talent near the top. The current workforce is aging out, and a lack of new trained talent is draining today’s manufacturers of reliable CNC programmers and their expert knowledge of manufacturing techniques. It’s causing a widening skills gap, but if you’re a shop owner or manager, you probably already know this. You’ll also be aware that a lack of experience costs time and money in both your design and manufacturing processes.
You might not know that a smarter solution to the experience problem exists. When looking to replace the loss in CAM expertise, what if you used your existing design and engineering teams (who have little or no CAM training) to help fill the gap rather than adding more people to your team?
While this sounds like an ‘‘easier said than done’’ scenario, it’s not impossible. After all, if there was a way to capture lost expert knowledge, your team could easily compensate for the lack of know-how by automating and standardizing processes.
This thinking leads to new possibilities with clear advantages for workflow. The first advantage is bringing critical manufacturing in-house, which will help control quality and reduce manufacturing costs exponentially. Other benefits include a better understanding of manufacturing processes during the design phase and a faster development cycle, which manufacturers of every size need.
As these advantages become clearer, the critical question changes from “Could my design and engineering teams fill the gap?” to “What tools will allow me to do this?”
Harness the Power of Knowledge-Based Machining
Knowledge-Based Machining (or KBM) is a relatively new term that is rapidly gaining significance in manufacturing circles. While a single, concise definition has yet to be decided on, it generally refers to a CAM software’s ability to make essential knowledge a part of its automation. The system’s knowledge is then translated directly into “smart” features, which help streamline and strengthen the design process, potentially eliminating or severely reducing the need to manage and document changes.
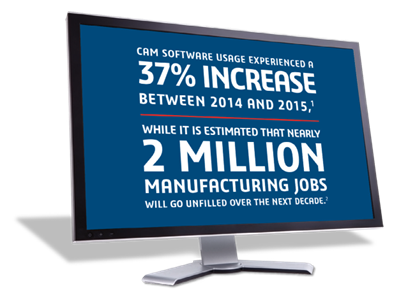
As CAM usage rises and the number of people coming in continues to drop, shop owners and team managers will need a reliable way to make up the difference.
Smart and Deeply Integrated CAM Tools
Knowledge-based Machining is at the heart of SOLIDWORKS® CAM, a new add-in that was introduced with the launch of SOLIDWORKS 2018. Powered by the industry-leading technology of CAMWorks™ and available at all levels of SOLIDWORKS CAD, SOLIDWORKS CAM is an easy-to-use 2.5-axis milling and turning solution which allows users to program in either part or assembly environments.
SOLIDWORKS CAM Stands Apart for a Number of Reasons
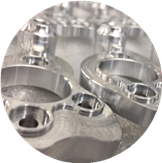
It’s connected to SOLIDWORKS design tools
Direct or “deep” integration allows SOLIDWORKS CAM to take advantage of the information in your 3D CAD model, so it’s easy for your team to make better, more-informed decisions.
It utilizes tolerance-based machining
Use SOLIDWORKS Model-Based Definition (MBD) to ensure machining strategies are automatically adjusted based on tolerance specifications.
It easily standardizes processes
While SOLIDWORKS CAM can be used like any other CAM software—setting up operations, picking tools, setting speeds and feeds—the real advantage is running SOLIDWORKS CAM in the automated mode (also called “rules-based” Machining).
A New Way to Automate With “Rules-Based” Machining
Proven machining strategies, or rules, embedded into the software, allow for faster toolpath creation—in many cases, five to ten times faster. These rules are included out of the box and can be easily modified while the CAM user is programming by simply changing the parameters and clicking save.
In essence, rules-based Machining is like having a built-in manufacturing consultant help make team decisions. It allows novice CAM users to get up to speed quickly by automating the tedious and repetitive tasks associated with most mainstream CAM software. It also aids experienced users by allowing them to program much faster.
Ultimately, this technology can be transformative because it allows manufacturers to automate the design-to-manufacturing process fully. It also opens the door for new “build to order” possibilities, with custom parts that are automatically designed and programmed. What has traditionally required hours of engineering and CAM programming time can now be automatically designed and programmed in seconds.
Machining Strategies in Use
According to a survey conducted by Geometric, over 32 percent of top shops are currently using machining strategies for turning processes.
All Shops | Top Shops | Other Shops | |
High-Speed Machining | 46.6% | 54.1% | 44.7% |
Hard Turning | 34.3% | 32.4% | 34.8% |
Hard Milling | 28.7% | 27.0% | 29.1% |
Large-Part Machining | 27.0% | 35.1% | 24.8% |
More Power. More Capabilities.
More Than Just a Smarter Approach to Manufacturing
Bring your manufacturing processes into the new age of automation with SOLIDWORKS. Discover powerful tools and features, including SOLIDWORKS CAM that will help revolutionize your design-to-manufacturing process on a single, unified platform.
Contact Us
Have a question? We’re always available to talk over the phone at 262-790-1080, for you to leave a message or for you to submit a request – just contact us.
Share
Meet the Author