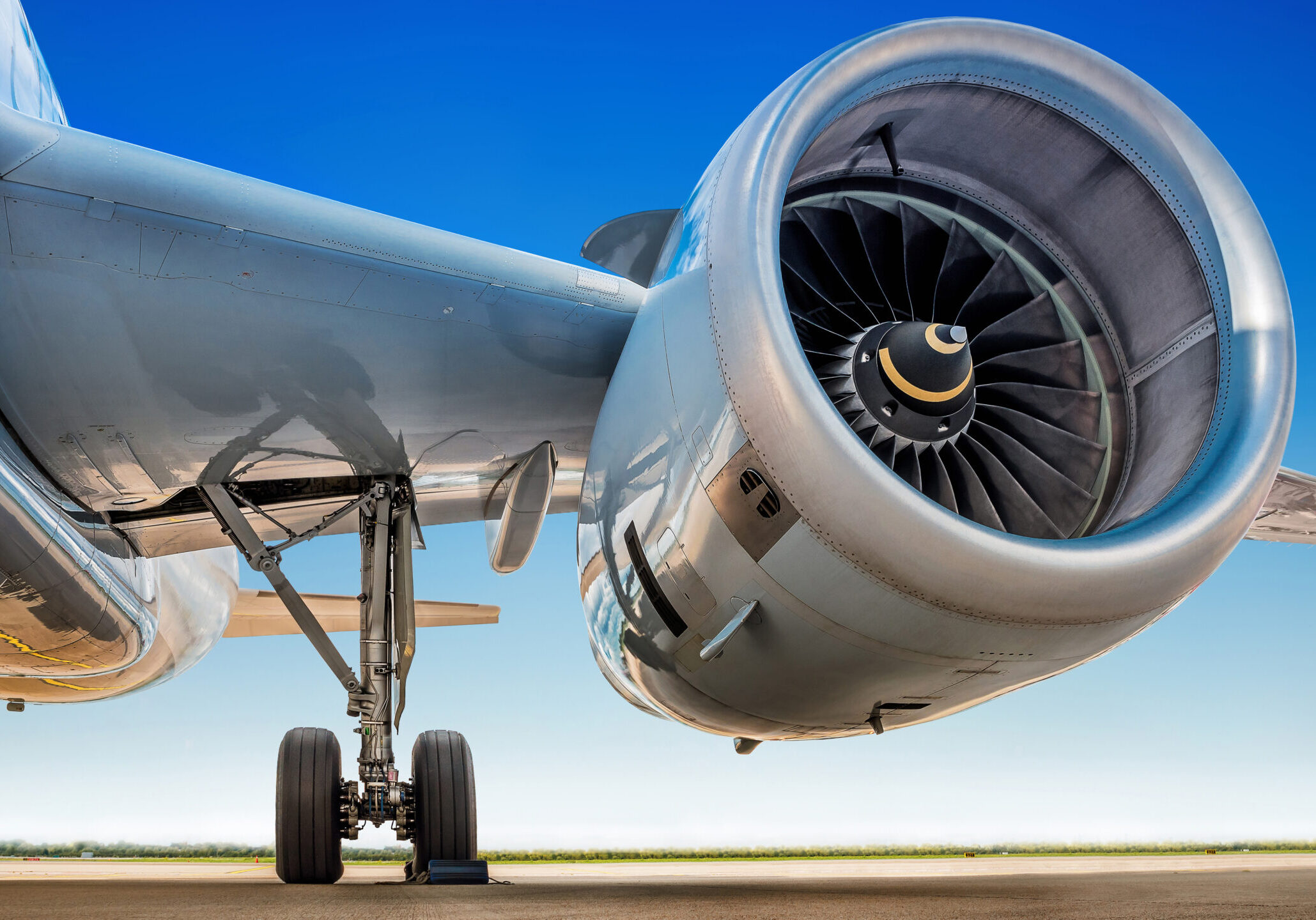
Across the Aerospace & Defense industry, rising customer expectations along with growing program complexity make it more challenging to compete. As systems become more complex to design, build, and deliver, OEMs and suppliers need to accelerate innovation, drive efficiencies, and move to the factory of the future to allow for greater agility in production rate. This requires a new way to conceptualize, design, manufacture, test, certify and sustain new air and space vehicles.

SOLIDWORKS Simulation for Aerospace Applications
Aerospace and defense components must withstand extreme conditions such as high loads, vibrations, and temperature variations while maintaining structural integrity. SIMULIA software offers sophisticated finite element analysis (FEA) tools that enable engineers to simulate and validate the structural performance of parts and assemblies under these demanding conditions.
Example: Suppose a manufacturing engineer is tasked with designing an aircraft wing spar for a military aircraft. By using SIMULIA software, they can simulate the behavior of the wing spar under different loads, including aerodynamic forces during flight and G-forces during maneuvers. The software can predict stress distribution, deformation, and fatigue life, allowing engineers to optimize the design for maximum strength and durability.
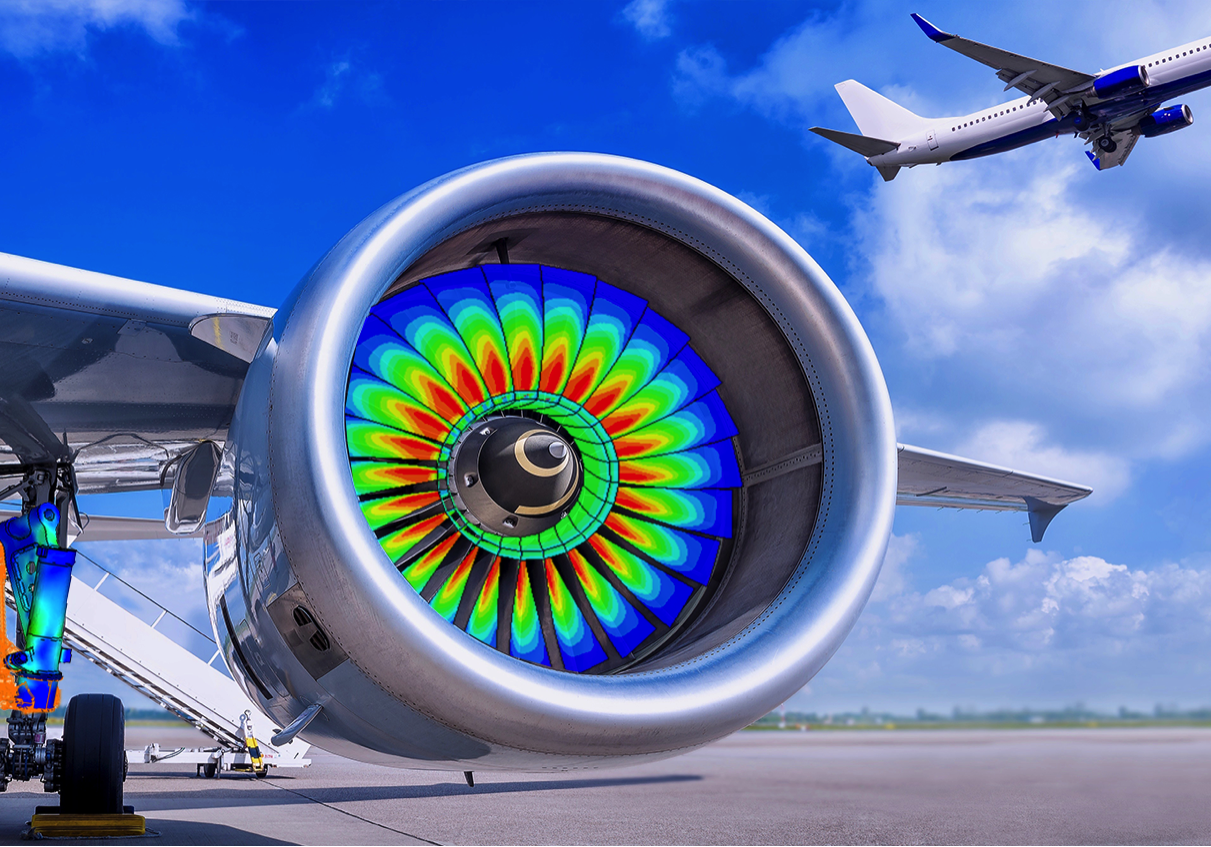
Effective thermal management is critical to ensure the reliable operation of electronic systems, propulsion components, and other critical equipment. SIMULIA software provides tools for thermal analysis, allowing engineers to simulate heat transfer, thermal gradients, and thermal stresses within complex assemblies.
Example: Consider a manufacturing engineer tasked with designing a thermal management system for a satellite payload. Using SIMULIA software, they can model the satellite's structure, heat sources, and heat dissipation mechanisms. By simulating thermal behavior under different operating conditions, engineers can optimize the placement of heat sinks, insulation materials, and cooling channels to prevent overheating and ensure the payload operates within specified temperature limits.
Many aerospace and defense systems involve interactions between multiple physical phenomena, such as structural mechanics, fluid dynamics, and electromagnetic effects. SIMULIA software offers multi-physics simulation capabilities that enable engineers to analyze these complex interactions comprehensively.
Example: Imagine a manufacturing engineer tasked with developing a guided missile system. Using SIMULIA software, they can simulate the aerodynamic performance of the missile during flight, including factors like drag, lift, and stability. Additionally, they can analyze the structural response of the missile body to aerodynamic forces and assess how electromagnetic interference from onboard electronics affects guidance systems. By integrating these analyses into a unified simulation framework, engineers can optimize the missile design for accuracy, reliability, and performance.

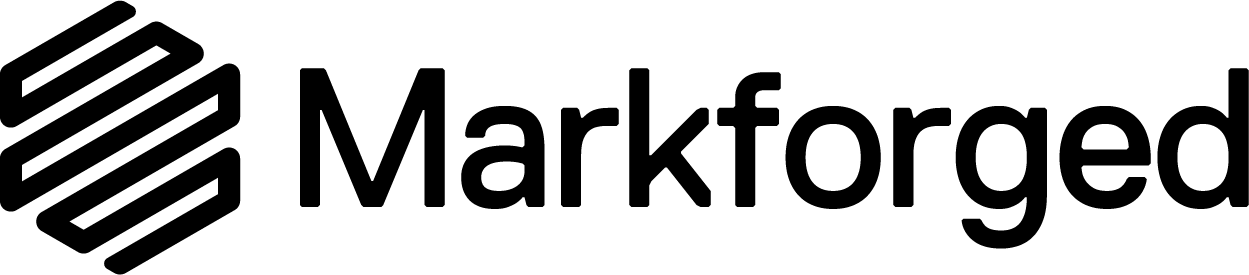
Additive Manufacturing with Composites in Aerospace and Defense
From on-demand MRO and spare parts in commercial aviation to innovation in Urban Air Mobility, aerospace industry leaders are improving responsiveness to rapidly shifting supply chains and labor availability with Additive Manufacturing.
The Digital Forge gives modern manufacturers the simplest way to build with materials they already know. Fabricate end-use carbon fiber composites unattended, overnight. Skip multi-week lead times and expedite fees for metal and composite prototypes, tools, and fixtures.

Aerospace Ready 3D Printing Materials
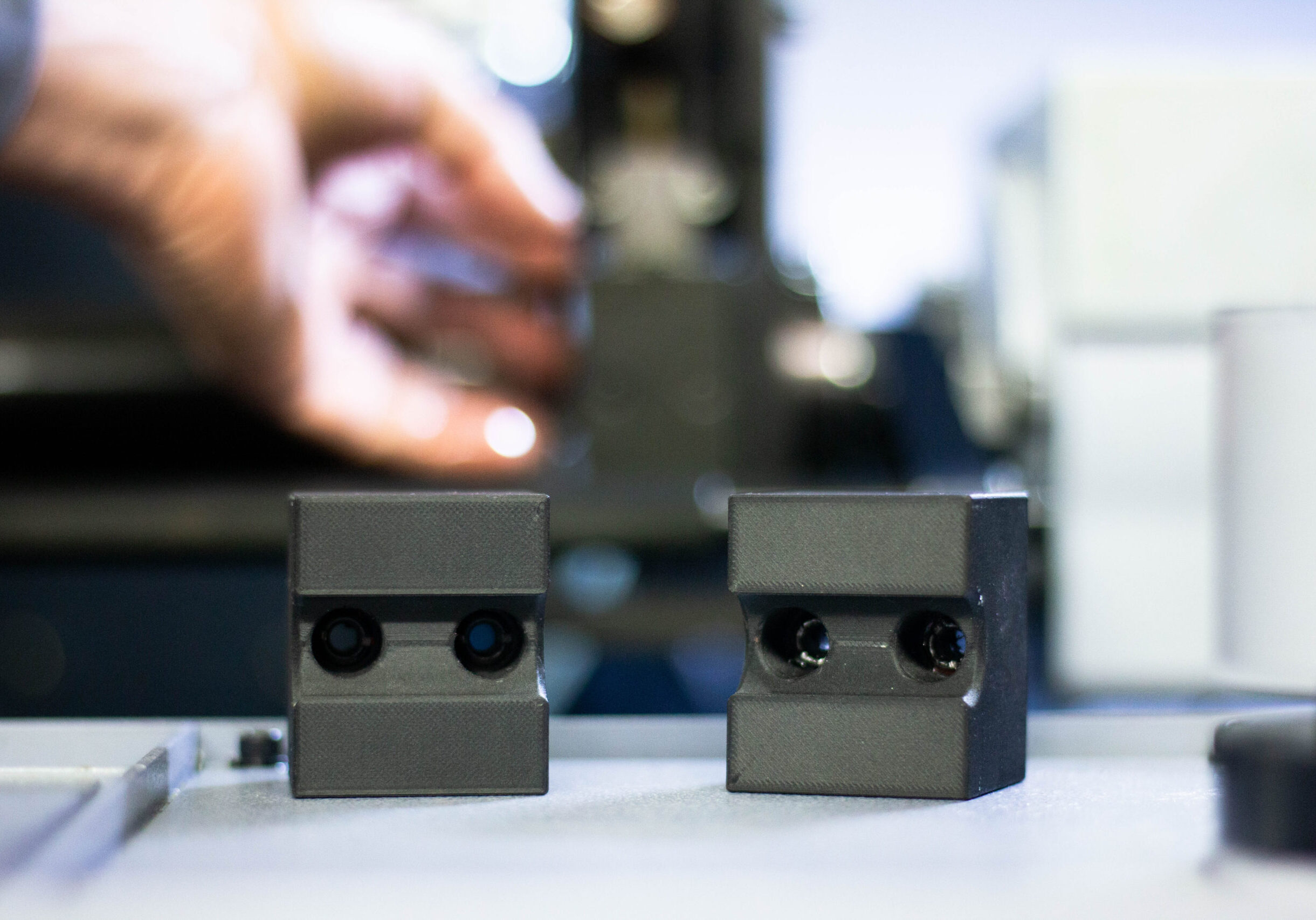
Onyx FR-A
Onyx FR is a flame-retardant short carbon fiber filled nylon designed for use in applications where parts must resist burning.
Applications:
- Weld Fixturing
- Aerospace Clips & Brackets
- Laser Marking Fixtures
- Energy/Electrical Brackets & Fixtures
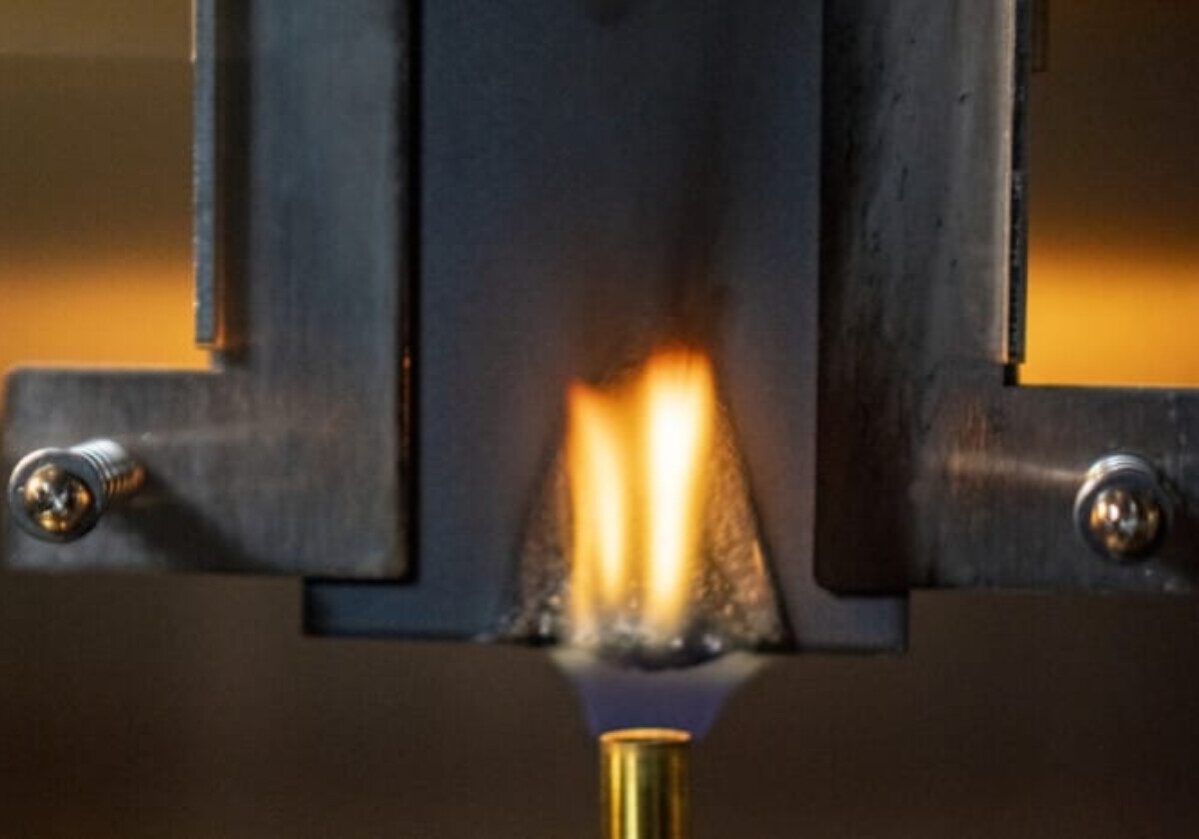
Carbon Fiber FR-A
A flame-retardant variant of Markforged’s unique, ultra-high-strength Continuous Carbon Fiber.
Applications:
- Cabin Components
- Brackets & Mounts
- MRO & Spare Parts
- End-Use Parts
- Functional Prototypes
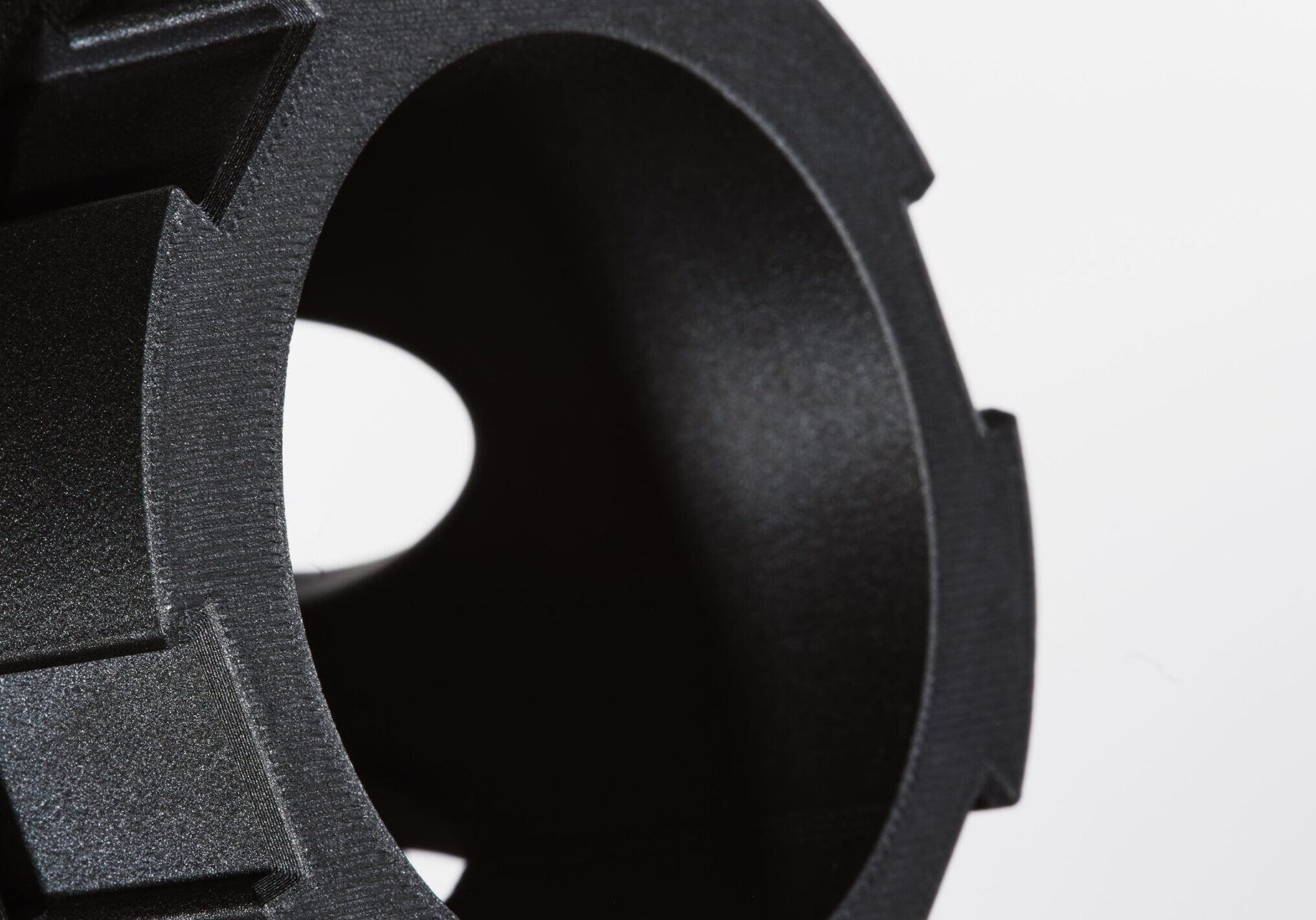
Vega
Vega, Markforged’s high-performance carbon fiber-filled PEKK, 3D prints critical aerospace parts with aluminum strength and a smooth black matte finish, ideal for minimal post-processing.
Applications:
- Aircraft Brackets, Handles, and Knobs
- Non-critical structural aerospace parts
- High temperature tooling
- Custom aerospace ducting
3D Printing for Aerospace
Read the eBook 3D printing composites for aerospace.
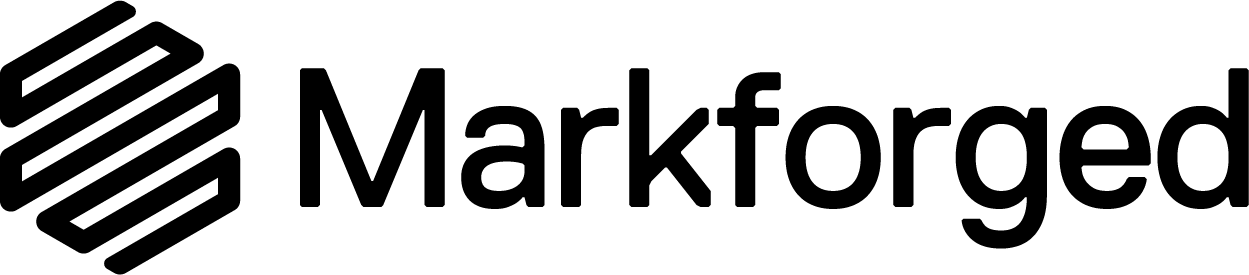
Start creating high-quality, intricate patterns while reducing production time and costs
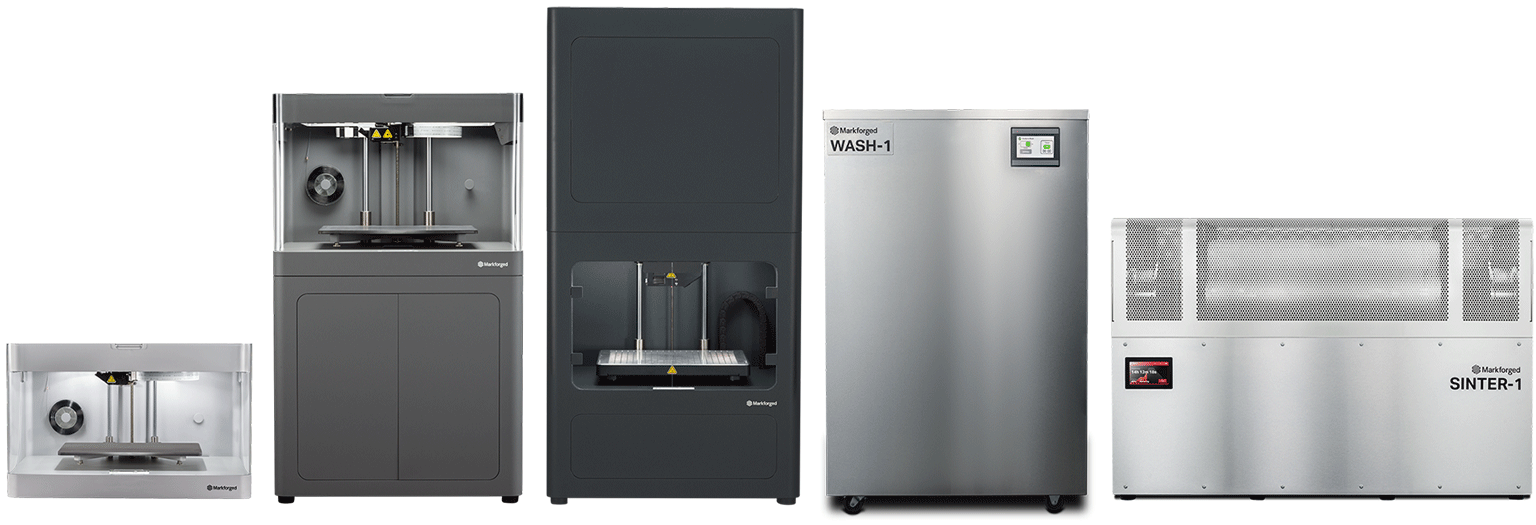